AS5045 AB austriamicrosystems, AS5045 AB Datasheet
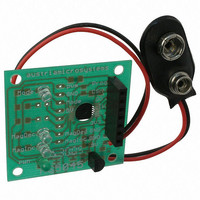
AS5045 AB
Specifications of AS5045 AB
Related parts for AS5045 AB
AS5045 AB Summary of contents
Page 1
... PWM outputs simultaneously Ideal for applications in harsh environments due to contactless position sensing No calibration required Figure 1. Typical Arrangement of AS5045 and Magnet www.austriamicrosystems.com 3 Key Features Contactless high resolution rotational position encoding over a full turn of 360 degrees Two digital 12bit absolute outputs: - Serial interface and ...
Page 2
... Changing the PWM Frequency...............................................................................................................17 10 Analog Output ........................................................................................................................................17 11 Programming the AS5045 ......................................................................................................................18 11.1 Zero Position Programming....................................................................................................................18 11.2 Repeated OTP Programming .................................................................................................................18 11.3 Non-permanent Programming ................................................................................................................19 11.4 Analog Readback Mode .........................................................................................................................20 12 Alignment Mode ..................................................................................................................................... Operation ...............................................................................................................................22 14 Choosing the Proper Magnet..................................................................................................................23 14.1 Physical Placement of the Magnet .........................................................................................................24 www.austriamicrosystems.com Revision 1.7 2 – 33 ...
Page 3
... Angular Error Caused by Propagation Delay ..........................................................................................29 17.5 Internal Timing Tolerance.......................................................................................................................29 17.6 Temperature ..........................................................................................................................................30 17.6.1 Magnetic Temperature Coefficient ..........................................................................................................30 17.7 Accuracy over Temperature ...................................................................................................................30 17.7.1 Timing Tolerance over Temperature .......................................................................................................30 18 Package Drawings and Markings ...........................................................................................................31 19 Ordering Information ..............................................................................................................................31 20 Recommended PCB Footprint ................................................................................................................32 www.austriamicrosystems.com Revision 1.7 3 – 33 ...
Page 4
... By using an external low pass filter, the digital PWM signal is converted into an analog voltage, making a direct replacement of potentiometers possible. Table 1. Pin Description Pin Symbol Type 1 MagINCn DO_OD 2 MagDECn DO_OD www.austriamicrosystems.com 1 16 MagINCn MagDECn Mode ...
Page 5
... Sampling Selectable by MODE input pin: frequency 2.5kHz, 10kHz www.austriamicrosystems.com Description Must be left unconnected Select between slow (low, VSS) and fast (high, VDD5V) mode. Internal pull-down resistor. Negative Supply Voltage (GND) OTP Programming Input and Data Input for Daisy Chain mode. Internal pull- down resistor (~74kΩ ...
Page 6
... Body temperature (Lead-free package) Humidity non-condensing 6.3 Operating Conditions Parameter Ambient temperature Supply current Supply voltage at pin VDD5V Voltage regulator output voltage at pin VDD3V3 Supply voltage at pin VDD5V Supply voltage at pin VDD3V3 www.austriamicrosystems.com Symbol Min Max VDD5V -0.3 7 VDD3V3 5 VDD5V V -0 ...
Page 7
... Open drain leakage current 6.4.4 CMOS Output: PWM (operating conditions -40 to +125°C, VDD5V = 3.0-3.6V (3V operation) VDD5V = 4.5-5.5V (5V operation) amb unless otherwise noted) Parameter High level output voltage Low level output voltage Output current www.austriamicrosystems.com Symbol Min Max V 0.7 * VDD5V IH V 0.3 * VDD5V IL V ...
Page 8
... Magnetic input field B pk amplitude Magnetic offset B off Field non-linearity Input frequency f (rotational speed of mag_abs magnet) Displacement radius Disp Eccentricity Ecc Recommended magnet material and temperature drift www.austriamicrosystems.com Symbol Min Max V VDD5V –0 VSS+0 Min Typ Max Unit Note Recommended magnet: Ø 6mm x 2.5mm for cylindrical magnets 2 ...
Page 9
... Power-up time System propagation delay absolute output : delay of ADC, DSP and absolute interface Internal sampling rate for absolute output: Internal sampling rate for absolute output Read-out frequency www.austriamicrosystems.com Min Typ Max RES INL ± 0.5 opt INL ± 0.9 temp INL ± ...
Page 10
... CLK FE register Start of data output T CLK / 2 Data output valid t DO valid Data output tristate t DO tristate Pulse width of CSn t CSn Read-out frequency f CLK www.austriamicrosystems.com Actual curve TN Ideal curve DNL+1LSB INL 0.09° 2048 180° Min Typ Max Unit 100 ns 500 ns ...
Page 11
... CLK pulse width Hold time of Vprog after programming Programming voltage, pin PROG Programming voltage off level Programming current Analog read CLK Programmed Zener voltage (log.1) Unprogrammed Zener voltage (log. 0) www.austriamicrosystems.com Min Typ Max 232 244 256 220 244 268 0.95 1 1.05 ...
Page 12
... Pulse Width Modulated signal at pin 12 (PWM). This PWM signal output also allows the generation of a direct proportional analogue voltage, by using an external Low-Pass-Filter. The AS5045 is tolerant to magnet misalignment and magnetic stray fields due to differential measurement technique and Hall sensor conditioning circuitry. Figure 4. AS5045 Block Diagram www.austriamicrosystems.com Revision 1.7 12 – 33 ...
Page 13
... OCF, COF, LIN, Parity and Magnetic Field status (increase/decrease). A subsequent measurement is initiated by a “high” pulse at CSn with a minimum duration of t www.austriamicrosystems.com Slow Mode (Mode = low) 2.61 kHz (384 µs) ≤ 0.03° rms 384µ ...
Page 14
... INCn DECn 0 0 Off 0 1 Off When bit MagCompEn is programmed in the OTP, the function of status bits MagINC, MagDec and pins MagINCn, MagDECn is changed to the following function: www.austriamicrosystems.com Mag Mag Parity INC DEC Even checksum of bits 1: 1*) 1*) OTP: Mag CompEn = 0 (default) Mag ...
Page 15
... The last data bit of the first device (Parity) is followed by a dummy bit and the first data bit of the second device (D11), etc… (see Figure 7) Figure 6. Daisy Chain Hardware Configuration www.austriamicrosystems.com OTP: Mag CompEn = 1 (red-yellow-green programming option) Mag ...
Page 16
... Position off The PWM frequency is internally trimmed to an accuracy of ±5% (±10% over full temperature range). This tolerance can be cancelled by measuring the complete duty cycle as shown above. Figure 8. PWM Output Signal www.austriamicrosystems.com Angular Position Data Angle PW MIN 0 deg (Pos 0) 1µs ...
Page 17
... Figure 9 shows an example of a simple passive low pass filter to generate the analog output. R1, R2 ≥ 4k7 C1, C2 ≥ 1µ should be ≥4k7 to avoid loading of the PWM output. Larger values of Rx and Cx will provide better filtering and less ripple, but will also slow down the response time. www.austriamicrosystems.com Symbol Typ Unit f ...
Page 18
... However, a bit that has already been programmed should not be programmed twice. Therefore it is recommended that bits that are already programmed are set to “0” during a programming cycle. www.austriamicrosystems.com ) must be applied to program the fuses (Figure 11). To exit the PROG ...
Page 19
... See Application Note AN5000-20 for further information. Figure 10. Programming Access – Write Data (section of Figure 11 atain rog ena ble t D atain valid Figure 11. Complete Programming Sequence www.austriamicrosystems.com clk se e text Z ero P o sitio n Revision 1 ...
Page 20
... A reading between 100mV and 1V indicates a faulty bit, which may result in an undefined digital value, when the OTP is read at power-up. th Following the 18 clock (after reading bit “ccw”), the chip must be reset by disconnecting the power supply. www.austriamicrosystems.com Revision 1.7 , that ref , and the resulting ref 20 – ...
Page 21
... The alignment mode can be reset to normal operation by a power-on-reset (disconnect / re-connect power supply falling edge on CSn with Prog = low. Figure 14. Enabling the Alignment Mode Prog AlignMode enable CSn 2µs 2µs min. min. www.austriamicrosystems.com Analog Readback Data at PROG V V programmed ref Mag PWM PWM Z0 ...
Page 22
... A buffer capacitor of 100nF is recommended in both cases close to pin VDD5V. Note that pin VDD3V3 must always be buffered by a capacitor. It must not be left floating, as this may cause an instable internal 3.3V supply voltage which may lead to larger than normal jitter of the measured angle. www.austriamicrosystems.com 3.3V Operation 2.2...10µF ...
Page 23
... The magnet’s field strength should be verified using a gauss-meter. The magnetic field B a concentric circle with a radius of 1.1mm (R1), should be in the range of ±45mT…±75mT (see Figure 17). Figure 17. Typical Magnet (6x3mm) and Magnetic Field Distribution N R1 Vertical field component www.austriamicrosystems.com typ. 6mm diameter S Magnet axis Vertical field Magnet axis component ...
Page 24
... Larger distances are possible, as long as the required magnetic field strength stays within the defined limits. However, a magnetic field outside the specified range may still produce usable results, but the out-of-range condition will be indicated by MagINCn (pin 1) and MagDECn (pin 2), see Table 1. Figure 19. Vertical Placement of the Magnet Die surface www.austriamicrosystems.com 3 Defined ...
Page 25
... A ratiometric division of the sine and cosine vectors removes the need for an accurate absolute magnitude of the magnetic field and thus accurate Z-axis alignment of the magnetic source. The recommended differential input range of the magnetic field strength (B the die. In addition to this range, an additional offset of ±5mT, caused by unwanted external stray fields is allowed. www.austriamicrosystems.com ° ...
Page 26
... For each misalignment step, the measurement as shown in is repeated and the accuracy (Err 0.25° in) is entered as the Z-axis in the 3D-graph. www.austriamicrosystems.com )/2 is specified as better than ±0.5 – Err ...
Page 27
... Figure 22. Example of Linearity Error over 360° 0.5 0.4 0.3 0.2 0 109 163 217 -0.1 -0.2 -0.3 -0.4 -0.5 www.austriamicrosystems.com Linearity Error over XY-misalignment [° ° Linearity error with centered magnet [degrees] Err max 271 325 379 433 ...
Page 28
... The upper speed limit in slow mode is ~6.000rpm and ~30.000rpm in fast mode. The only restriction at high speed is that there will be fewer samples per revolution as the speed increases (see Table 2). Regardless of the rotational speed, the absolute angular value is always sampled at the highest resolution of 12 bit. www.austriamicrosystems.com *1 in slow mode (pin MODE = low or Revision 1.7 28 – ...
Page 29
... Position off www.austriamicrosystems.com ) and the time it takes the external control unit to read and process the angular delay also have the same tolerance as the internal oscillator (see above). off is used to measure the angle, the resulting value also has this timing tolerance. on Revision 1.7 ...
Page 30
... The only concern to the user is the width of the PWM output pulse, which relates directly to the timing tolerance of the internal oscillator. This influence however can be cancelled by measuring the complete PWM duty cycle instead of just the PWM pulse (see 17.5). www.austriamicrosystems.com Revision 1.7 30 – 33 ...
Page 31
... Ordering Information Delivery: Tape and Reel (1 reel = 2000 devices) Tubes (1 box = 100 tubes à 77 devices) Order # AS5045ASSU for delivery in tubes Order # AS5045ASST for delivery in tape and reel www.austriamicrosystems.com Marking: YYWWIZZ Y: Last Digit of Manufacturing Year inch WW: Manufacturing Week Min Typ Max I: Plant Identifier ...
Page 32
... AS5045 Data Sheet 20 Recommended PCB Footprint Figure 24. Recommended PCB Footprint Table 8. Recommended Footprint Data Recommended Footprint Data mm A 9.02 0.355 B 6.16 0.242 C 0.46 0.018 D 0.65 0.025 E 5.01 0.197 www.austriamicrosystems.com inch Revision 1.7 32 – 33 ...
Page 33
... AG for each application. The information furnished here by austriamicrosystems AG is believed to be correct and accurate. However, austriamicrosystems AG shall not be liable to recipient or any third party for any damages, including but not limited to personal injury, property damage, loss of profits, loss of use, interruption of business or indirect, special, incidental or consequential damages, of any kind, in connection with or arising out of the furnishing, performance or use of the technical data herein ...