OPF794 Optek, OPF794 Datasheet - Page 22
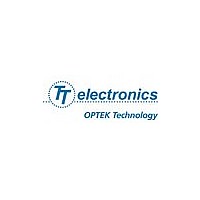
OPF794
Manufacturer Part Number
OPF794
Description
Photodiodes Pin Photodiode
Manufacturer
Optek
Datasheet
1.OPF794.pdf
(135 pages)
Specifications of OPF794
Maximum Reverse Voltage
100 V
Maximum Rise Time
6 ns
Mounting Style
SMD/SMT
Product
Photodiode
Lead Free Status / RoHS Status
Lead free / RoHS Compliant
Available stocks
Company
Part Number
Manufacturer
Quantity
Price
Light Emitting Diodes (LEDs)
L
O
D
Page B—2
Product Definitions
EADERSHIP IN
IODE
UTPUT
OPTEK remains unchallenged as the industry’s most complete high quality source for infrared emitters. The latest state-of-the-art
solution grown epitaxial techniques are used to produce high quality GaAs and GaAlAs diode materials required to make OPTEK
infrared emitting diodes. This precision processing ensures high junction emission efficiency and long operating life with minimal
degradation. The added benefit of over 30 years of mounting, bonding, and packaging experience makes OPTEK the undisputed
technological leader in the design and production of infrared emitting diodes.
When engineers are asked which features they value most in OPTEK’s electronic components, the answers most often given are
quality and reliability. Assuring high quality is a philosophy that begins at product conception and is carried through the design
phase and is heavily emphasized during every step in the manufacture of OPTEK infrared emitting diodes.
The outputs of the vast majority of OPTEK emitters are specified using apertured radiant incidence, Ee(APT), expressed in
milliwatts per square centimeter. This method, also known as on-axis intensity measurement, provides the best accuracy and
convenience for the design engineer. Production testing consists of measuring 100 percent of the energy passing through a
specified diameter aperture orthogonal to the optical axis, and a specified distance from the device. For OPTEK devices, the
distance chosen for this measurement is equivalent to the typical operating distance from emitter to sensor. Most specifications
for compatible photosensors describe output current at a specified radiant intensity, also expressed in milliwatts per square
centimeter. Therefore, the design of close proximity transmissive emitter/sensor assemblies can be done more accurately, and
with a minimum of optical calculations and specification conversions.
Infrared emitter manufacturers use three methods of specifying output limits on infrared emitters. These are Radiant Power
Output (PO), Radiant Intensity (Ie) and Apertured Radiant Incidence [Ee(APT)]. Radiant Power Output (PO) sometimes called Total
Power, is strictly interpreted as a measure of the total energy emitted from the device. OPTEK has interpreted this to include only
the energy useful to most customers. Therefore, side and backward emissions are not measured. As a benchmark for
comparison among devices, OPTEK devices are conservatively rated. For example, The PO reading for the useful portion of the
OP295A radiation pattern is 60 percent higher when a parabolic reflector is used to capture normally unused side emissions as
opposed to OPTEK’s more conservative rating method. When making PO comparisons among manufacturers, the design
engineer should always investigate the method of measurement.
Radiant intensity (Ie) is usually expressed in milliwatts per steradian. This method attempts to account for useable energy, where
the peak intensity falls within an included angle centered around the optical axis. Through some moderately complex
geometrical calculations, the energy falling on the sensor can be roughly estimated if the sensor is on or close to the optical axis
and if the distance from emitter to sensor is known. However, most infrared emitters can not accurately be modeled as a point
source at the close proximity used in many applications (less than four inches); therefore, this method has the potential to result
in serious design errors. Additionally, it is more cumbersome than OPTEK’s direct approach of characterizing emitters in terms of
apertured radiant incidence.
Gallium arsenide (GaAs) and gallium aluminum arsenide (GaAlAs) each have specific advantages when used in the manufacture
of OPTEK infrared emitters. GaAs emits energy at 935 ± 15 nanometers while GaAlAs emits at 890 ± 20 nanometers. As
temperature increases, these peaks shift upward by 0.26 and 0.20 nanometers per degree centigrade, respectively. Due to the
spectral matching with photosensitive silicon, which exhibits a sensitivity maximum of 850 nanometers, GaAlAs has the
advantage of more efficient coupling. The sensor is better able to “see” the energy emitted by GaAlAs. In addition, at
equivalent forward currents, GaAlAs is typically a more efficient emitter of infrared energy.
M
S
ATERIAL
PECIFICATIONS
M
ANUFACTURING
S
ELECTION
D
ESIGNED FOR
E
NGINEERING
Issue A.1 2005
OPTEK Technology Inc. www.optekinc.com