SP400-0.009-00-11 Bergquist, SP400-0.009-00-11 Datasheet - Page 5
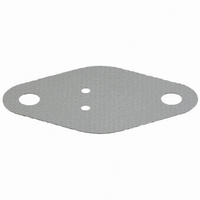
SP400-0.009-00-11
Manufacturer Part Number
SP400-0.009-00-11
Description
THERMAL PAD TO-3 .009" SP400
Manufacturer
Bergquist
Series
Sil-Pad® 400r
Specifications of SP400-0.009-00-11
Usage
TO-3, TO-66
Shape
Rhombus
Outline
33.32mm x 19.35mm
Thickness
0.009" (0.229mm)
Backing, Carrier
Fiberglass
Color
Gray
Thermal Resistivity
1.40°C/W
Thermal Conductivity
0.9 W/m-K
Lead Free Status / RoHS Status
Lead free / RoHS Compliant
Adhesive
-
Other names
7403-09FR-11
BER218
BER218
Improve Durability and Performance
Thermal Clad improves durability because designs can be kept
simple while components are kept cool. The low thermal
impedance of the Thermal Clad dielectric outperforms other
insulators for power components, allowing for cooler operation.
Thermal Clad keeps assemblies cool by eliminating thermal
interfaces and using thermally efficient solder joints. Voltage
breakdown and thermal performance improve in potted assem-
blies using SMD’s and bare die on Thermal Clad.
Thermal Clad can also reduce production costs by enabling
automated pick-and-place equipment for SMD’s.
The Anatomy Of A Thermal Clad Board
Thermal Clad is a dielectric (ceramic-polymer blend) coated metal
base with a bonded copper circuit layer.This unique material offers
superior heat transfer to help cool components while eliminating
the problems associated with fragile ceramics. Different than others,
Bergquist doesn’t use fiberglass, allowing for better thermal perfor-
mance.
Thermal Clad is a three layer system comprised of the following:
t
t
t
Base Layer
Dielectric Layer:
mum thermal resistance. Glass carriers degrade thermal perfor-
mance which is why our dielectrics are glass-free. CML is the one
exception because of its prepreg form, a glass carrier is needed
for handling purposes. The dielectric layer is the key element of
Thermal Clad, and bonds the base metal and circuit metal
together. The dielectric has U.L. recognition, simplifying agency
acceptance of final assemblies.
Base Layer:
copper may also be used. The most widely used base material
thickness is 0.062" (1.57mm) in aluminum, although many thick-
nesses are available. In some applications, the base layer of metal
may not be needed. See “Specialty Applications” on page 11.
Circuit Layer:
1oz. to 10oz. (35-350µm) in standard Thermal Clad.
Dielectric Layer
Circuit Layer
This is often aluminum, but other metals such as
This is the printed circuit foil with a thickness of
This offers electrical isolation with mini-
Reduce Board Size and Replace Hardware
Thermal Clad greatly reduces board space while replacing other
components including heat sinks. It offers the opportunity to
eliminate mica and grease or rubber insulators under power
devices by using direct solder mount to Thermal Clad. By elimi-
nating this hardware, heat transfer is improved.
Interconnects can be eliminated by using etched traces on the
Thermal Clad board. In fact, whole sections of PWB’s are often
eliminated. It permits the use of surface mount power and
passive devices to reduce real estate. With Thermal Clad, many
discrete devices can be replaced at the board level.
Bergquist’s manufacturing facility located in Prescott, Wisconsin features state-of-the-art
process capabilities. Process manufacturing uses the latest in technology including
environmental clean room control, surface finishing, coating and lamination.
3