SIC417CD-T1-E3 Vishay, SIC417CD-T1-E3 Datasheet - Page 13
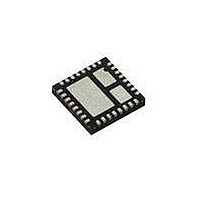
SIC417CD-T1-E3
Manufacturer Part Number
SIC417CD-T1-E3
Description
IC DRIVER MOSF SYNC BUCK 55MLPQ
Manufacturer
Vishay
Series
microBUCK™r
Datasheet
1.SIC417CD-T1-E3.pdf
(20 pages)
Specifications of SIC417CD-T1-E3
Topology
Step-Down (Buck) Synchronous (1), Linear (LDO) (1)
Function
Any Function
Number Of Outputs
2
Frequency - Switching
200kHz ~ 1MHz
Voltage/current - Output 1
0.5 V ~ 5.5 V, 10A
Voltage/current - Output 2
0.75 V ~ 5.25 V, 150mA
W/led Driver
No
W/supervisor
No
W/sequencer
No
Voltage - Supply
3 V ~ 28 V
Operating Temperature
-25°C ~ 125°C
Mounting Type
*
Package / Case
*
Output Voltage
0.5 V to 5.5 V
Output Current
10 A
Input Voltage
3 V to 28 V
Switching Frequency
200 KHz to 1 MHz
Mounting Style
SMD/SMT
Duty Cycle (max)
95 %
Primary Input Voltage
28V
No. Of Outputs
1
Voltage Regulator Case Style
MLPQ
No. Of Pins
32
Operating Temperature Range
-25°C To +125°C
Svhc
No SVHC
Rohs Compliant
Yes
Lead Free Status / RoHS Status
Lead free / RoHS Compliant
Lead Free Status / RoHS Status
Lead free / RoHS Compliant, Lead free / RoHS Compliant
Available stocks
Company
Part Number
Manufacturer
Quantity
Price
Part Number:
SIC417CD-T1-E3
Manufacturer:
VISHAY/威世
Quantity:
20 000
Frequency Selection
Selection of the switching frequency requires making a
trade-off between the size and cost of the external filter
components (inductor and output capacitor) and the power
conversion efficiency.
The desired switching frequency is 250 kHz which results
from using component selected for optimum size and cost.
A resistor (R
setting the frequency) using the following equation.
To select R
use the value associated with maximum V
t
Substituting for R
R
Inductor Selection
In order to determine the inductance, the ripple current must
first be defined. Low inductor values result in smaller size but
create higher ripple current which can reduce efficiency.
Higher inductor values will reduce the ripple current and
voltage and for a given DC resistance are more efficient.
However, larger inductance translates directly into larger
packages and higher cost. Cost, size, output ripple, and
efficiency are all used in the selection process.
The ripple current will also set the boundary for power-save
operation. The switching will typically enter power-save
mode when the load current decreases to 1/2 of the ripple
current. For example, if ripple current is 4 A then power-save
operation will typically start for loads less than 2 A. If ripple
current is set at 40 % of maximum load current, then power-
save will start for loads less than 20 % of maximum current.
The inductor value is typically selected to provide a ripple
current that is between 25 % to 50 % of the maximum load
current. This provides an optimal trade-off between cost,
efficiency, and transient performance.
During the DH on-time, voltage across the inductor is
(V
shown next.
Example
In this example, the inductor ripple current is set equal to
50 % of the maximum load current. Thus ripple current will be
50 % x 10 A or 5 A. To find the minimum inductance needed,
use the V
A slightly larger value of 0.88 µH is selected. This will
decrease the maximum I
Document Number: 69062
S10-1367-Rev. D, 14-Jun-10
ON
TON
IN
= 318 ns at 13.2 V
-V
= 154.9 kΩ, use R
OUT
IN
). The equation for determining inductance is
TON
and T
TON
L =
, use the maximum value for V
R
) is used to program the on-time (indirectly
ton
TON
ON
(13.2 - 1.05) x 318 ns
t
=
L =
ON
values that correspond to V
(t
results in the following solution
IN
ON
=
(V
, 1.05 V
25 pF x V
TON
RIPPLE
IN
5 A
- 10 ns) x V
V
INMAX.
- V
I
= 154 kΩ.
RIPPLE
V
OUT
OUT
to 4.4 A.
OUT
OUT
x f
) x t
SW
IN
, 250 kHz
ON
= 77 µH
IN
.
IN
, and for t
INMAX.
ON
Note that the inductor must be rated for the maximum DC
load current plus 1/2 of the ripple current. The ripple current
under minimum V
following equations.
Capacitor Selection
The output capacitors are chosen based on required ESR
and capacitance. The maximum ESR requirement is
controlled by the output ripple requirement and the DC
tolerance. The output voltage has a DC value that is equal to
the valley of the output ripple plus 1/2 of the peak-to-peak
ripple. Change in the output ripple voltage will lead to a
change in DC voltage at the output.
The design goal is that the output voltage regulation be
± 4 % under static conditions. The internal 500 mV reference
tolerance is 1 %. Allowing 1 % tolerance from the FB resistor
divider, this allows 2 % tolerance due to V
Since this 2 % error comes from 1/2 of the ripple voltage, the
allowable ripple is 4 %, or 42 mV for a 1.05 V output.
The maximum ripple current of 4.4 A creates a ripple voltage
across the ESR. The maximum ESR value allowed is shown
by the following equations.
The output capacitance is usually chosen to meet transient
requirements. A worst-case load release, from maximum
load to no load at the exact moment when inductor current is
at the peak, determines the required capacitance. If the load
release is instantaneous (load changes from maximum to
zero in < 1 µs), the output capacitor must absorb all the
inductor's stored energy. This will cause a peak voltage on
the capacitor according to the following equation.
Assuming a peak voltage V
load release), and a 10 A load release, the required
capacitance is shown by the next equation.
If the load release is relatively slow, the output capacitance
can be reduced. At heavy loads during normal switching,
when the FB pin is above the 500 mV reference, the DL
T
I
I
RIPPLE
RIPPLE_VIN
ON_VINMIN
ESR
ESR
COUT
COUT
COUT
=
MAX
MAX
(V
IN
MIN
=
=
IN
=
= 9.5 mΩ
MIN
MIN
(10.8 - 1.05) x 384 ns
conditions is also checked using the
25 pF x R
I
- V
=
RIPPLEMAX
V
=
= 595 µF
L (I
OUT
RIPPLE
L
0.88 µH (10 +
OUT
0.88 µH
(V
PEAK
) x T
V
(1.15)
PEAK
INMIN
TON
+
ON
=
1
2
of 1.150 (100 mV rise upon
)
2
x V
2
x I
42 mV
- (1.05)
4.4 A
- (V
Vishay Siliconix
RIPPLEMAX
OUT
1
2
OUT
x 4.4)
2
= 4.25 A
)
OUT
2
2
www.vishay.com
)
2
ripple.
SiC417
13