LT1952EGN-1#PBF Linear Technology, LT1952EGN-1#PBF Datasheet - Page 14
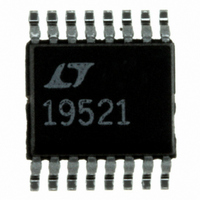
LT1952EGN-1#PBF
Manufacturer Part Number
LT1952EGN-1#PBF
Description
IC CTLR PWM SGL SWITCH 16-SSOP
Manufacturer
Linear Technology
Datasheet
1.LT1952EGNPBF.pdf
(24 pages)
Specifications of LT1952EGN-1#PBF
Pwm Type
Current Mode
Number Of Outputs
1
Frequency - Max
560kHz
Duty Cycle
90%
Voltage - Supply
6.82 V ~ 25 V
Buck
No
Boost
No
Flyback
Yes
Inverting
No
Doubler
No
Divider
No
Cuk
No
Isolated
Yes
Operating Temperature
-40°C ~ 125°C
Package / Case
16-SSOP
Frequency-max
560kHz
Lead Free Status / RoHS Status
Lead free / RoHS Compliant
Available stocks
Company
Part Number
Manufacturer
Quantity
Price
APPLICATIONS INFORMATION
LT1952/LT1952-1
Blanking is provided in 2 phases (Figure 6): The fi rst phase
automatically blanks during gate rise time. Gate rise times
can vary depending on MOSFET type. For this reason the
LT1952/LT1952-1 perform true ‘leading edge blanking’ by
automatically blanking OC and I
until OUT rises to within 0.5V of V
level of 13V. The second phase of blanking starts after
the leading edge of OUT has been completed. This phase
is programmable by the user with a resistor connected
from the BLANK pin to ground. Typical durations for this
portion of the blanking period are from 45ns at R
= 10k to 540ns at R
be approximated as:
(see graph in Typical Performance Characteristics)
Programming Current Limit (OC Pin)
The LT1952/LT1952-1 use a precise 107mV sense threshold
at the OC pin to detect overcurrent conditions in the
converter and set a soft-start latch. It is independent of
duty cycle because it is not affected by slope compensation
programmed at the I
peak current in the primary MOSFET by sensing the
voltage across a sense resistor (R
14
OUT
BLANKING
Blanking (extended) = [45(R
(AUTOMATIC)
BLANKING
LEADING
0
EDGE
Figure 6. Leading Edge Blank Timing
Xns X + 45ns
R
= 10k
(MIN)
BLANK
BLANK
SENSE
10k < R
(PROGRAMMABLE)
= 120k. Blanking duration can
pin. The OC pin monitors the
EXTENDED
BLANKING
BLANK
SENSE
BLANK
IN
240k
or reaches its clamp
S
comparator outputs
/10k)]ns
[X + 45(R
) in the source of
CURRENT
BLANK
SENSE
DELAY
100ns
/10k)]ns
BLANK
1952 F06
the MOSFET. The current limit for the converter can be
programmed by:
where:
Programming Slope Compensation
The LT1952/LT1952-1 use a current mode architecture
to provide fast response to load transients and to ease
frequency compensation requirements. Current mode
switching regulators which operate with duty cycles above
50% and have continuous inductor current must add slope
compensation to their current sensing loop to prevent
subharmonic oscillations. (For more information on slope
compensation, see Application Note 19.) The LT1952/
LT1952-1 have programmable slope compensation to allow
a wide range of inductor values, to reduce susceptibility
to PCB generated noise and to optimize loop bandwidth.
The LT1952/LT1952-1 program slope compensation by
inserting a resistor R
(Figure 7). The LT1952/LT1952-1 generate a current at
the I
maximum duty cycle of the OUT pin. A simple calculation
of I(I
at the I
(See both graphs ‘I
‘I
Performance Characteristics section.)
SENSE
Current limit = (107mV/R
R
I
N
N
RIPPLE
S
S
P
SENSE
SENSE
= sense resistor in source of primary MOSFET
= number of transformer secondary turns
= number of transformer primary turns
LT1952-1
SENSE
LT1952/
CURRENT SLOPE = 35μA • DC
Maximum Threshold vs Duty Cycle’ in the Typical
Figure 7. Programming Slope Compensation
I
SENSE
= p-p ripple current in the output inductor L1
) • R
pin which is linear from 0% duty cycle to the
OUT
1952 F07
OC
pin for programmable slope compensation.
SLOPE
R
SLOPE
SENSE
gives an added ramp to the voltage
SLOPE
V
R
Pin Current vs. Duty Cycle’ and
S
S
in series with the I
S
V
I
DC = DUTY CYCLE
FOR SYNC OPERATION
I
k = f
SENSE
SENSE(SYNC)
)(N
(ISENSE)
OSC
P
= 8μA + 35DC μA
/N
/f
SYNC
= V
S
S
) – (1/2)(I
= 8μA + (k • 35DC)μA
+ (I
SENSE
• R
SLOPE
SENSE
RIPPLE
)
19521fd
)
pin