XW2Z-200J-B9 Omron, XW2Z-200J-B9 Datasheet - Page 59
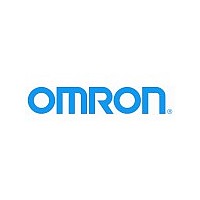
XW2Z-200J-B9
Manufacturer Part Number
XW2Z-200J-B9
Description
CONNECTOR CABLE 2M
Manufacturer
Omron
Datasheet
1.XW2Z-200J-C1.pdf
(504 pages)
Specifications of XW2Z-200J-B9
Lead Free Status / Rohs Status
Lead free / RoHS Compliant
Other names
XW2Z200JB9
- Current page: 59 of 504
- Download datasheet (9Mb)
Function Tables Arranged by Purpose
32
Synchronous
control
Speed control
Purpose
Slave axis con-
trol synchro-
nized to virtual
axis.
Control of a par-
ticular axis oper-
ation at a speed
with a uniform
ratio applied
Creating any
trapezoidal
speed control
pattern (e.g., S-
curve accelera-
tion/decelera-
tion) (fine
control of accel-
eration/deceler-
ation using time)
Electronic cam:
Changing target
position and
speed every
cycle based on
virtual pulse out-
put (position or
speed) to exe-
cute positioning.
Electronic gear
operation: Pulse
outputs based
on input pulses
multiplied by a
set factor.
Electronic cam
operation:
Changing target
position and
speed every
cycle according
to time axis and
perform posi-
tioning.
Operation
• Virtual axis
• Cam curve
• Pulse output
• Constant cycle
• High-speed
• Straight-line
• Pulse outputs
• Constant cycle
• Cam curve
• Pulse output
• Constant cycle
Main functions
(AXIS instruc-
tion)
generation or
cam curve
table every
cycle based on
ladder pro-
gramming
(APR instruc-
tion)
with specified
target position
and frequency
(PULS(886)
instruction)
time
counter PV
table (APR
instruction)
with specified
target position
and frequency
(PULS(886)
instruction)
time
generation or
cam curve
table every
cycle based on
ladder pro-
gramming
(APR instruc-
tion)
with specified
target position
and frequency
(PULS(886)
instruction)
time
used
7-8 Virtual Pulse Output Function
Execute pulse output control of slave axis based
on virtual axis position and speed using AXIS
instruction, instead of high-speed counter PV for
real axis outlined above.
Instead of the slave axis operation reflecting the
real machinery operation outlined above, this
method is used to operate position control for
multiple axes using the same timing.
7-6-13 Pulse Output Function Procedures
Set pulse output operating mode to electronic
cam control (circular).
Prepare a straight line table whose slope
becomes the multiplier for APR instruction and
use APR instructions to calculate the pulse out-
put target position for slave axis corresponding
to high-speed counter PV and executes pulse
output control.
Speed is set and controlled to enable distribution
of specified number of pulses within FQM1 con-
trol cycle.
7-6-13 Pulse Output Function Procedures
Set pulse output operation mode to electronic
cam control mode (linear) or electronic cam con-
trol mode (circular).
Used for applications such as creating ideal Ser-
vomotor control patterns.
Makes the Motion Control Module cycle time
constant, generates a time axis using ladder
programming, specifies the target position and
speed for the Servo Driver of the slave axis
based on that time axis and gives pulse outputs.
The time unit can be set to milliseconds, allow-
ing fine control in FQM1 high-speed cycles.
Details
Section 1-7