XW2Z-200J-B9 Omron, XW2Z-200J-B9 Datasheet - Page 66
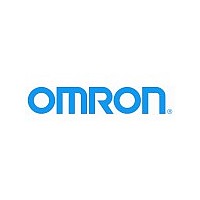
XW2Z-200J-B9
Manufacturer Part Number
XW2Z-200J-B9
Description
CONNECTOR CABLE 2M
Manufacturer
Omron
Datasheet
1.XW2Z-200J-C1.pdf
(504 pages)
Specifications of XW2Z-200J-B9
Lead Free Status / Rohs Status
Lead free / RoHS Compliant
Other names
XW2Z200JB9
- Current page: 66 of 504
- Download datasheet (9Mb)
Functions Changed from FQM1-CM001 to FQM1-CM002)
Functions Changed from FQM1-MMP21/MMA21 to FQM1-MMP22/MMA22
Comparison with Functions in Earlier Models
Comment Memory
(built-in flash mem-
ory)
Free running timers
added to enable cal-
culating time inter-
vals without using
timer instructions
Support for CJ-
series Units
Creating data links
with the PLC over an
open network
Serial PLC Link func-
tion supports the
Complete Link
Method
Increase in the DM
Area words automat-
ically saved to flash
memory
DM Area data reten-
tion
Changing accelera-
tion, deceleration,
and target value dur-
ing acceleration or
deceleration for
ACC(888)
Function
Function
Function
Comments are stored in flash memory built into the FQM1. The fol-
lowing comment and section information can be read and written.
• Symbol table files (CX-Programmer symbol names and I/O com-
• Comment files (CX-Programmer line comments and annotations)
• Program index files (CX-Programmer section names, section com-
Free running timers have been added in the Auxiliary Area (A000 and
A001) as system timers that operate after power is turned ON.
A000 is reset to 0000 hex at startup and is incremented by 1 every
10 ms. When it reaches FFFF hex (655,350 ms), it returns to 0 in a
ring operation and continues timing.
A001 is reset to 0000 hex at startup and is incremented by 1 every
100 ms. When it reaches FFFF hex (6,553,500 ms), it returns to 0 in
a ring operation and continues timing.
Example: The difference between the value of A000 at process time
A and the value of A000 at process time B can be calculated to mea-
sure the time (in 10-ms increments) between process A and process
B without using a timer instruction.
CJ-series Units can be used by mounting an FQM1-IC101 I/O Con-
trol Module. There are some limitations on the models of CJ-series
Units that can be mounted. See the reference sections for details.
A CJ1W-DRM21 DeviceNet Master Unit can be mounted in the
FQM1 to use the FQM1 as a DeviceNet Slave. Data can be
exchanged without programming by establishing a data link from a
host PLC (such as a CJ1M) that has a DeviceNet Master mounted.
Note The FQM1 supports the CJ1W-DRM21 Master Unit in Slave
The Serial PLC Link function can use both the Complete Link Method
and Master Link Method.
With the Complete Link Method, the CJ1M CPU Unit and FQM1 can
perform program-free data exchange with all other nodes.
For the FQM1-CM001, D30000 to D32767 are automatically saved to
flash memory when they are written to using the DM transfer function
or from a PT and then the data in flash memory is automatically
restored to the DM Area the next time power is turned ON.
These words have been increased to D20000 to D32767 in the
FQM1-CM002.
A control bit operation can save part of the Motion Control Module’s
DM Area (D00000 to D29999) to flash memory. The saved DM Area
data can be restored automatically at startup when the system set-
tings are set to restore the data.
Previously, the acceleration, deceleration, and target speed could not
be changed during pulse output acceleration or deceleration for
ACC(888). This is possible with the new versions.
ACC(888) can also be used in the same way during analog outputs
to change the slop or the output value setting during sloped outputs.
ments)
ments, and program comments)
mode only. The Master Unit cannot be used in Master mode.
Specification
Specification
Specification
5-7-4 Comment Memory
Function
D-1 Auxiliary Area Alloca-
tions in Order of Address
6-2 I/O Allocation to CJ-
series Units, 6-3 Data
Exchange between Coordi-
nator Module and Units
6-2 I/O Allocation to CJ-
series Units, 6-3 Data
Exchange between Coordi-
nator Module and Units, B-8
DeviceNet Area
6-1-4 Serial PLC Links
6-4 Automatic DM Data
Backup Function
7-11 DM Data Storage
Function
7-6-15 Pulse Output Start-
ing Conditions
7-10-4 Applicable Instruc-
tions
Reference
Reference
Reference
Section 1-8
39