IR3503MTRPBF International Rectifier, IR3503MTRPBF Datasheet - Page 13
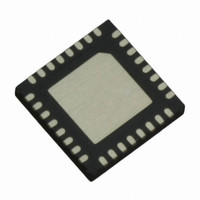
IR3503MTRPBF
Manufacturer Part Number
IR3503MTRPBF
Description
IC CTRL XPHASE VR11.0/1 32-MLPQ
Manufacturer
International Rectifier
Series
XPhase3™r
Datasheet
1.IR3503MTRPBF.pdf
(39 pages)
Specifications of IR3503MTRPBF
Applications
Processor
Current - Supply
8mA
Voltage - Supply
4.75 V ~ 7.5 V
Operating Temperature
0°C ~ 100°C
Mounting Type
Surface Mount
Package / Case
*
Package
32-Lead MLPQ
Circuit
X-Phase Control IC
Switch Freq (khz)
250kHz to 1.5MHz
Pbf
PbF Option Available
Lead Free Status / RoHS Status
Lead free / RoHS Compliant
Other names
IR3503MTRPBFTR
Since the voltage drop in the body diode is often comparable to the output voltage, the inductor current slew rate can
be increased significantly. This patented technique is referred to as “body braking” and is accomplished through the
“body braking comparator” located in the phase IC. If the error amplifier’s output voltage drops below the output voltage
of the share adjust amplifier in the phase IC, this comparator turns off the low side gate driver, enabling the bottom
FET body diode to take over. There is 100mV upslope and 200mV down slope hysteresis for the body braking
comparator.
Lossless Average Inductor Current Sensing
Inductor current can be sensed by connecting a series resistor and a capacitor network in parallel with the inductor and
measuring the voltage across the capacitor, as shown in Figure 7. The equation of the sensing network is,
Usually the resistor Rcs and capacitor Ccs are chosen, such that, the time constant of Rcs and Ccs equals the time
constant of the inductor, which is the inductance L over the inductor DCR R
voltage across Ccs will be proportional to the current through L, and the sense circuit can be treated as if only a sense
resistor with the value of R
inductor DC current, but affects the AC component of the inductor current.
The advantage of sensing the inductor current versus high side or low side sensing is that actual output current being
delivered to the load is obtained rather than peak or sampled information about the switch currents. The output voltage
can be positioned to meet a load line based on real time information. Except for a sense resistor in series with the
inductor, this is the only sense method that can support a single cycle transient response. Other methods provide no
information during either load increase (low side sensing) or load decrease (high side sensing).
An additional problem associated with peak or valley current mode control for voltage positioning is that they suffer
from peak-to-average errors. These errors will show in many ways but one example is the effect of frequency variation.
If the frequency of a particular unit is 10% low, the peak to peak inductor current will be 10% larger and the output
impedance of the converter will drop by about 10%. Variations in inductance, current sense amplifier bandwidth, PWM
propagation delay, any added slope compensation, input voltage, and output voltage are all additional sources of peak-
to-average errors.
Page 13 of 39
Figure 8: Inductor Current Sensing and Current Sense Amplifier
L
was used. The mismatch of the time constants does not affect the measurement of
v
CSOUT
C
(
s
)
=
v
Current
Sense Amp
L
T
(
SLEW
s
)
1
i
+
L
=
sR
L
V
1
CS
O
( *
L
R
C
+
C
S
I
CS
V
MAX
v
BODYDIODE
L
=
R
C
v
S
−
i
L
C
c
L
C
S
I
(
s
MIN
)
1
)
+
R
sR
V
L
O
+
CS
C
sL
C
O
CS
L
. If the two time constants match, the
February 12, 2010
IR3503