ISL6522BIBZ Intersil, ISL6522BIBZ Datasheet - Page 10
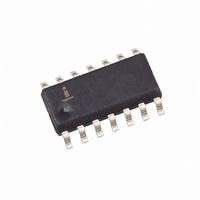
ISL6522BIBZ
Manufacturer Part Number
ISL6522BIBZ
Description
IC PWM BUCK BST VM 14SOIC
Manufacturer
Intersil
Datasheet
1.ISL6522BCBZ.pdf
(15 pages)
Specifications of ISL6522BIBZ
Pwm Type
Voltage Mode
Number Of Outputs
1
Frequency - Max
1MHz
Duty Cycle
100%
Voltage - Supply
10.8 V ~ 13.2 V
Buck
Yes
Boost
Yes
Flyback
No
Inverting
No
Doubler
No
Divider
No
Cuk
No
Isolated
No
Operating Temperature
-40°C ~ 85°C
Package / Case
14-SOIC (3.9mm Width), 14-SOL
Frequency-max
1MHz
Lead Free Status / RoHS Status
Lead free / RoHS Compliant
Available stocks
Company
Part Number
Manufacturer
Quantity
Price
Company:
Part Number:
ISL6522BIBZ-T
Manufacturer:
INTERSIL
Quantity:
9 100
Figure 8 shows an asymptotic plot of the DC-DC converter’s
gain vs. frequency. The actual modulator gain has a high
gain peak due to the high Q factor of the output filter and is
not shown in Figure 8. Using the above guidelines should
give a compensation gain similar to the curve plotted. The
open loop error amplifier gain bounds the compensation
gain. Check the compensation gain at F
capabilities of the error amplifier. The closed loop gain is
constructed on the log-log graph of Figure 8 by adding the
modulator gain (in dB) to the compensation gain (in dB). This
is equivalent to multiplying the modulator transfer function to
the compensation transfer function and plotting the gain.
The compensation gain uses external impedance networks
Z
loop. A stable control loop has a gain crossing with
-20dB/decade slope and a phase margin greater than 45
degrees. Include worst case component variations when
determining phase margin.
Component Selection Guidelines
Output Capacitor Selection
An output capacitor is required to filter the output and supply
the load transient current. The filtering requirements are a
function of the switching frequency and the ripple current.
The load transient requirements are a function of the slew
rate (di/dt) and the magnitude of the transient load current.
These requirements are generally met with a mix of
capacitors and careful layout.
Modern microprocessors produce transient load rates above
1A/ns. High frequency capacitors initially supply the transient
3. Place 2
4. Place 1
5. Place 2
6. Check Gain against Error Amplifier’s Open-Loop Gain
7. Estimate Phase Margin - Repeat if Necessary
FIGURE 8. ASYMPTOTIC BODE PLOT OF CONVERTER GAIN
FB
100
-20
-40
-60
80
60
40
20
and Z
0
10
(R2/R1)
20LOG
IN
MODULATOR
ND
ST
ND
to provide a stable, high bandwidth (BW) overall
100
Pole at the ESR Zero
Zero at Filter’s Double Pole
Pole at Half the Switching Frequency
GAIN
1K
F
Z1
F
FREQUENCY (Hz)
LC
F
Z2
10K
10
F
P1
F
(V
ESR
100K
IN
20LOG
F
/∆V
P2
OSC
P2
OPEN LOOP
ERROR AMP GAIN
1M
)
with the
COMPENSATION
GAIN
CLOSED LOOP
GAIN
10M
ISL6522B
and slow the current load rate seen by the bulk capacitors.
The bulk filter capacitor values are generally determined by
the ESR (effective series resistance) and voltage rating
requirements rather than actual capacitance requirements.
High frequency decoupling capacitors should be placed as
close to the power pins of the load as physically possible. Be
careful not to add inductance in the circuit board wiring that
could cancel the usefulness of these low inductance
components. Consult with the manufacturer of the load on
specific decoupling requirements. For example, Intel
recommends that the high frequency decoupling for the
Pentium-Pro be composed of at least forty (40) 1.0µF
ceramic capacitors in the 1206 surface-mount package.
Use only specialized low-ESR capacitors intended for
switching-regulator applications for the bulk capacitors. The
bulk capacitor’s ESR will determine the output ripple voltage
and the initial voltage drop after a high slew-rate transient.
An aluminum electrolytic capacitor’s ESR value is related to
the case size with lower ESR available in larger case sizes.
However, the equivalent series inductance (ESL) of these
capacitors increases with case size and can reduce the
usefulness of the capacitor to high slew-rate transient
loading. Unfortunately, ESL is not a specified parameter. Work
with your capacitor supplier and measure the capacitor’s
impedance with frequency to select a suitable component. In
most cases, multiple electrolytic capacitors of small case size
perform better than a single large case capacitor.
Output Inductor Selection
The output inductor is selected to meet the output voltage
ripple requirements and minimize the converter’s response
time to the load transient. The inductor value determines the
converter’s ripple current and the ripple voltage is a function
of the ripple current. The ripple voltage and current are
approximated by the following equations:
Increasing the value of inductance reduces the ripple current
and voltage. However, the large inductance values reduce
the converter’s response time to a load transient.
One of the parameters limiting the converter’s response to a
load transient is the time required to change the inductor
current. Given a sufficiently fast control loop design, the
ISL6522B will provide either 0% or 100% duty cycle in
response to a load transient. The response time is the time
required to slew the inductor current from an initial current
value to the transient current level. During this interval the
difference between the inductor current and the transient
current level must be supplied by the output capacitor.
Minimizing the response time can minimize the output
capacitance required.
∆I =
V
------------------------------- -
IN
Fs x L
- V
OUT
•
V
--------------- -
V
OUT
IN
∆V
OUT
= ∆I x ESR