MAX8632ETI+T Maxim Integrated Products, MAX8632ETI+T Datasheet - Page 12
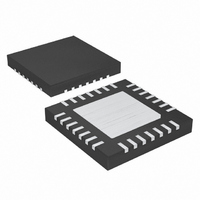
MAX8632ETI+T
Manufacturer Part Number
MAX8632ETI+T
Description
IC PWR SUPPLY DDR 28-TQFN
Manufacturer
Maxim Integrated Products
Datasheet
1.MAX8632ETIT.pdf
(29 pages)
Specifications of MAX8632ETI+T
Applications
Controller, DDR
Voltage - Input
2 ~ 28 V
Number Of Outputs
1
Voltage - Output
1.8V, 2.5V, 0.7 ~ 5.5 V
Operating Temperature
-40°C ~ 85°C
Mounting Type
Surface Mount
Package / Case
28-TQFN Exposed Pad
Output Voltage
1.8 V, 2.5 V, 0.7 V to 5.5 V
Output Current
15 A
Input Voltage
2 V to 28 V
Mounting Style
SMD/SMT
Maximum Operating Temperature
+ 85 C
Minimum Operating Temperature
- 40 C
Lead Free Status / RoHS Status
Lead free / RoHS Compliant
Integrated DDR Power-Supply Solution for
Desktops, Notebooks, and Graphic Cards
The MAX8632 combines a synchronous-buck PWM con-
troller, an LDO linear regulator, and a 10mA reference out-
put buffer. The buck controller drives two external
n-channel MOSFETs to deliver load currents up to 15A
and generate voltages down to 0.7V from a +2V to +28V
input. The LDO linear regulator can sink and source up to
1.5A continuous and 3A peak current with relatively fast
response. These features make the MAX8632 ideally
suited for DDR memory applications.
The MAX8632 buck regulator is equipped with a fixed
switching frequency of up to 600kHz using Maxim’s
proprietary constant on-time Quick-PWM architecture.
This control scheme handles wide input/output voltage
ratios with ease, and provides 100ns “instant-on”
response to load transients, while maintaining high effi-
ciency with relatively constant switching frequency.
The buck controller, LDO, and a reference output
buffer are provided with independent current limits.
Lossless foldback current limit in the buck regulator is
achieved by monitoring the drain-to-source voltage
drop of the low-side FET. The ILIM input is used to
adjust this current limit. Overvoltage protection, if
selected, is achieved by latching the low-side synchro-
nous FET on and the high-side FET off when the output
voltage is over 116% of its set output. It also features
an optional undervoltage protection by latching the
MOSFET drivers to the OFF state during an overcurrent
condition, when the output voltage is lower than 70% of
the regulated output. This helps minimize power dissi-
pation during a short-circuit condition.
The current limit in the LDO and buffered reference out-
put buffer is ±5A and ±32mA, respectively, and neither
have the over- or undervoltage protection. When the
current limit in either output is reached, the output no
longer regulates the voltage, but regulates the current
to the value of the current limit.
The MAX8632 requires an external +5V bias supply in
addition to the input voltage (V
ply external to the IC improves the efficiency and elimi-
nates the cost associated with the +5V linear regulator
that would otherwise be needed to supply the PWM cir-
cuit and the gate drivers. If stand-alone capability is
needed, then the +5V supply can be generated with an
external linear regulator such as the MAX1615. V
AV
source is a fixed +4.5V to +5.5V supply.
V
drivers, and AV
12
DD
DD
______________________________________________________________________________________
is the supply input for the buck regulator’s MOSFET
, and IN can be connected together if the input
+5V Bias Supply (V
DD
supplies the power for the rest of
Detailed Description
IN
). Keeping the bias sup-
DD
and AV
DD
DD
)
,
the IC. The current from the AV
supply must supply the current for the IC and the gate
drive for the MOSFETs. This maximum current can be
estimated as:
where I
into V
charges of MOSFETs Q1 and Q2 (at V
Figure 8, and f
The Quick-PWM control architecture is a pseudo-fixed-
frequency, constant on-time, current-mode regulator
with voltage feed-forward (Figure 1). This architecture
relies on the output filter capacitor’s ESR to act as a
current-sense resistor, so the output ripple voltage pro-
vides the PWM ramp signal. The control algorithm is
simple: the high-side switch on-time is determined
solely by a one-shot whose pulse width is inversely pro-
portional to input voltage and directly proportional to
the output voltage. Another one-shot sets a minimum
off-time of 300ns (typ). The on-time one-shot is trig-
gered if the error comparator is high, the low-side
switch current is below the valley current-limit thresh-
old, and the minimum off-time one-shot has timed out.
The heart of the PWM core is the one-shot that sets the
high-side switch on-time. This fast, low-jitter, adjustable
one-shot includes circuitry that varies the on-time in
response to input and output voltages. The high-side
switch on-time is inversely proportional to the input volt-
age (V
where K (the switching period) is set by the TON input
connection (Table 1) and R
tance of the synchronous rectifier (Q2) in Figure 8. This
algorithm results in a nearly constant switching fre-
quency despite the lack of a fixed-frequency clock
generator. The benefits of a constant switching fre-
quency are twofold:
1) The frequency can be selected to avoid noise-sensi-
2) The inductor ripple-current operating point remains
tive regions such as the 455kHz IF band.
relatively constant, resulting in an easy design
methodology and predictable output voltage ripple.
I
DD
BIAS
t
IN
ON
Free-Running Constant-On-Time PWM
VDD
) and is proportional to the output voltage:
and AV
=
=
+ I
K
I
SW
VDD
AVDD
×
DD
is the switching frequency.
(
V
+
OUT
, Q
are the quiescent supply currents
I
AVDD
G1
On-Time One-Shot (TON)
+
and Q
I
LOAD
+
DS(ON)Q2
f
SW
V
IN
G2
DD
×
×
(
R
Q
are the total gate
DS ON Q
and V
G
is the on-resis-
1
(
+
GS
)
Q
DD
G
2
= 5V) in
2
)
power
)