LTC1702IGN#TR Linear Technology, LTC1702IGN#TR Datasheet - Page 13
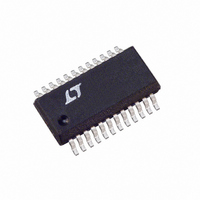
LTC1702IGN#TR
Manufacturer Part Number
LTC1702IGN#TR
Description
IC REG SW DUAL SYNC 2PH 24SSOP
Manufacturer
Linear Technology
Series
PolyPhase®r
Type
Step-Down (Buck)r
Datasheet
1.LTC1702CGN.pdf
(36 pages)
Specifications of LTC1702IGN#TR
Internal Switch(s)
No
Synchronous Rectifier
Yes
Number Of Outputs
2
Current - Output
1A, 25A
Frequency - Switching
550kHz
Voltage - Input
3 ~ 7 V
Operating Temperature
-40°C ~ 85°C
Mounting Type
Surface Mount
Package / Case
24-SSOP
Lead Free Status / RoHS Status
Contains lead / RoHS non-compliant
Voltage - Output
-
Power - Output
-
Available stocks
Company
Part Number
Manufacturer
Quantity
Price
APPLICATIONS
Any time QB is on and the current flowing to the output is
reasonably large, the SW node at the drain of QB will be
somewhat negative with respect to PGND. The LTC1702
senses this voltage and inverts it to allow it to compare the
sensed voltage with a positive voltage at the I
I
user to set the voltage at I
to ground. The LTC1702 compares the two inputs and
begins limiting the output current when the magnitude of
the negative voltage at the SW pin is greater than the
voltage at I
The current limit detector is connected to an internal g
amplifier that pulls a current from the RUN/SS pin propor-
tional to the difference in voltage magnitudes between the
SW and I
soft-start capacitor at RUN/SS, reducing the duty cycle
and controlling the output voltage until the current drops
below the limit. The soft-start capacitor needs to move a
fair amount before it has any effect on the duty cycle,
adding a delay until the current limit takes effect (Figure 4).
This allows the LTC1702 to experience brief overload
conditions without affecting the output voltage regulation.
The delay also acts as a pole in the current limit loop to
enhance loop stability. Larger overloads cause the soft-
start capacitor to pull down quickly, protecting the output
components from damage. The current limit g
includes a clamp to prevent it from pulling RUN/SS below
0.5V and shutting off the device.
Power MOSFET R
limiting the accuracy obtainable from the LTC1702 current
limit loop. Additionally, ringing on the SW node due to
parasitics can add to the apparent current, causing the
loop to engage early. The LTC1702 current limit is
designed primarily as a disaster prevention, “no blow up”
circuit, and is not useful as a precision current regulator.
It should typically be set around 50% above the maximum
expected normal output current to prevent component
tolerances from encroaching on the normal current range.
See the Current Limit Programming section for advice on
choosing a valve for R
MAX
pin includes a trimmed 10µA pull-up, enabling the
MAX
MAX
pins. This current begins to discharge the
.
DS(ON)
U
IMAX
varies from MOSFET to MOSFET,
MAX
INFORMATION
U
.
with a single resistor, R
W
MAX
m
U
amplifier
pin. The
IMAX
m
,
DISCONTINUOUS/Burst Mode OPERATION
Theory of operation
The LTC1702 switching logic has three modes of opera-
tion. Under heavy loads, it operates as a fully synchro-
nous, continuous conduction switching regulator. In this
mode of operation (“continuous” mode), the current in the
inductor flows in the positive direction (toward the output)
during the entire switching cycle, constantly supplying
current to the load. In this mode, the synchronous switch
(QB) is on whenever QT is off, so the current always flows
through a low impedance switch, minimizing voltage drop
and power loss. This is the most efficient mode of opera-
tion at heavy loads, where the resistive losses in the power
devices are the dominant loss term.
Continuous mode works efficiently when the load current
is greater than half of the ripple current in the inductor. In
a buck converter like the LTC1702, the average current in
the inductor (averaged over one switching cycle) is equal
to the load current. The ripple current is the difference
between the maximum and the minimum current during a
switching cycle (see Figure 5a). The ripple current
depends on inductor value, clock frequency and output
voltage, but is constant regardless of load as long as the
LTC1702 remains in continuous mode. See the Inductor
Selection section for a detailed description of ripple
current.
As the output load current decreases in continuous mode,
the average current in the inductor will reach a point where
it drops below half the ripple current. At this point, the
inductor current will reverse during a portion of the
switching cycle, or begin to flow from the output back to
the input. This does not adversely affect regulation, but
does cause additional losses as a portion of the inductor
current flows back and forth through the resistive power
switches, giving away a little more power each time and
lowering the efficiency. There are some benefits to allow-
ing this reverse current flow: the circuit will maintain
regulation even if the load current drops below zero (the
load supplies current to the LTC1702) and the output
LTC1702
13
1702fa