R88A-CRGB005C Omron, R88A-CRGB005C Datasheet - Page 56
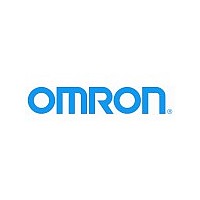
R88A-CRGB005C
Manufacturer Part Number
R88A-CRGB005C
Description
5M Encoder Cable CRGB
Manufacturer
Omron
Datasheet
1.XW2Z-050J-A31.pdf
(159 pages)
Specifications of R88A-CRGB005C
Lead Free Status / Rohs Status
Lead free / RoHS Compliant
Parameter
Unit No. Setting
Default Display
Control Mode Selection
Torque Limit Selection
Drive Prohibit Input
Selection
Command Speed
Selection
Zero Speed Designation/
Speed Command
Direction Switch
SP Selection
IM Selection
General-purpose Output
2 Selection
General-purpose Output
1 Selection
Operation Switch When
Using Absolute Encoder
RS-232 Baud Rate
Setting
RS-485 Baud Rate
Setting
Front Key Protection
Setting
R88A-RP02G : Parameter Unit Part Names
Function Selection Parameters
Parameter name
OMNUC G-series AC Servomotors/Servo Drives with General-purpose Pulse-string or Analog Inputs
Set the unit number.
Set the data to display on the Parameter Unit
when the power supply is turned ON.
Set the control mode to be used.
Set the torque limit method for forward and
reverse operation.
You can stop the Servomotor from rotating
beyond the device's travel distance range by
setting limit inputs.
Select the speed command when using speed
control.
Set the function of the Zero-speed Designation
Input (VZERO).
Select the relation between the output voltage
level and the speed.
Select the relation between the output voltage
level and the torque or number of pulses.
Assign the function of General-purpose Output 2
(OUTM2).
Assign the function of General-purpose Output 1
(OUTM1).
Set the operating method for the 17-bit absolute
encoder.
Select the baud rate for the RS-232 port.
Select the baud rate for RS-485
communications.
Front panel key operation can be limited to
Monitor Mode.
LED Display (6 Digits)
Unit No. Display (2 Digits)
Increment/Decrement Key
Mode Key
Shift Key
Data Key
If an error occurs, all digits will flash and the
display will switch to the error display.
Displays the selected Servo Drive's unit
number set in the Unit No. Setting (Pn00).
In Parameter Setting Mode, displays the 2-
digit parameter number.
Switches between the following six modes.
• Monitor Mode
• Parameter Setting Mode • Auxiliary Function Mode
• Parameter Write Mode • Copy Mode
Increases or decreases parameter numbers
or set values.
Shifts the digit being changed to the left.
Switches between the parameter and setting
displays, saves settings, etc.
Explanation
• Autotuning Mode
Position Loop Gain
Speed Loop Gain
Speed Loop Integration
Time Constant
Speed Feedback Filter
Time Constant
Torque Command Filter
Time Constant
Feed-forward Amount
Feed-forward Command
Filter
Position Loop Gain 2
Speed Loop Gain 2
Speed Loop Integration
Time Constant 2
Speed Feedback Filter
Time Constant 2
Torque Command Filter
Time Constant 2
Notch Filter 1 Frequency
Notch Filter 1 Width
Inertia Ratio
Realtime Autotuning
Mode Selection
Realtime Autotuning
Machine Rigidity
Selection
Adaptive Filter Selection
Vibration Filter Selection
Autotuning Operation
Setting
Overrun Limit Setting
Instantaneous Speed
Observer Setting
Notch Filter 2 Frequency
Notch Filter 2 Width
Notch Filter 2 Depth
Vibration Frequency 1
Vibration Filter 1 Setting
Vibration Frequency 2
Vibration Filter 2 Setting
Gain Parameters
Parameter name
Set to adjust position control system
responsiveness.
Set to adjust speed loop responsiveness.
Set to adjust the speed loop integration time
constant.
The encoder signal is converted to the speed
signal via the low pass filter.
Set to adjust the primary lag filter time constant
for the torque command section.
Set the position control feed-forward
compensation value.
Set the time constant of the primary lag filter
used in the speed feed-forward section.
Set to adjust position control system
responsiveness.
Set to adjust speed loop responsiveness.
Set to adjust the speed loop integration time
constant.
The encoder signal is converted to the speed
signal via the low pass filter.
Set to adjust the primary lag filter time constant
for the torque command section.
Set the notch frequency of the resonance
suppression notch filter.
Set the width to one of five levels for the
resonance suppression notch filter. Normally,
use the default setting.
Set the ratio between the mechanical system
inertia and the Servomotor rotor inertia.
Set the operating mode for realtime autotuning.
Set the machine rigidity to one of 16 levels
during realtime autotuning.
The higher the machine rigidity, the greater the
setting needs to be.
The higher the setting, the higher the
responsiveness.
When the Parameter Unit is used, 0 cannot be
set.
Enable or disable the adaptive filter.
Vibration filters 1 and 2 can be switched.
Set the operating pattern for autotuning.
Set the allowable operating range for the
Servomotor. The overrun limit function is
disabled if the parameter is set to 0.
Set the instantaneous speed observer.
Set the notch frequency of the resonance
suppression notch filter.
Set the notch filter width to one of five levels for
the resonance suppression notch filter. Normally,
use the default setting.
Set the depth of the resonance suppression
notch filter.
Set vibration frequency 1to suppress vibration at
the end of the load in dampening control.
Set vibration filter 1 to suppress vibration at the
end of the load in dampening control.
Set vibration frequency 2 to suppress vibration
at the end of the load in dampening control.
Set vibration filter 2 to suppress vibration at the
end of the load in dampening control.
R88M-G/R88D-GT
Explanation
59