HGTG11N120CND Fairchild Semiconductor, HGTG11N120CND Datasheet - Page 7
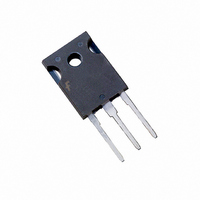
HGTG11N120CND
Manufacturer Part Number
HGTG11N120CND
Description
IGBT NPT N-CH 1200V 43A TO-247
Manufacturer
Fairchild Semiconductor
Datasheet
1.HGTG11N120CND.pdf
(8 pages)
Specifications of HGTG11N120CND
Igbt Type
NPT
Voltage - Collector Emitter Breakdown (max)
1200V
Vce(on) (max) @ Vge, Ic
2.4V @ 15V, 11A
Current - Collector (ic) (max)
43A
Power - Max
298W
Input Type
Standard
Mounting Type
Through Hole
Package / Case
TO-247-3
Configuration
Single
Collector- Emitter Voltage Vceo Max
1200 V
Collector-emitter Saturation Voltage
2.1 V
Maximum Gate Emitter Voltage
+/- 20 V
Continuous Collector Current At 25 C
43 A
Gate-emitter Leakage Current
+/- 250 nA
Power Dissipation
298 W
Maximum Operating Temperature
+ 150 C
Continuous Collector Current Ic Max
43 A
Minimum Operating Temperature
- 55 C
Mounting Style
Through Hole
Transistor Type
IGBT
Dc Collector Current
43A
Collector Emitter Voltage Vces
2.4V
Power Dissipation Pd
298W
Collector Emitter Voltage V(br)ceo
1.2kV
Transistor Case Style
TO-247
No. Of Pins
3
Svhc
No SVHC
Rohs Compliant
Yes
Channel Type
N
Collector-emitter Voltage
1.2kV
Collector Current (dc) (max)
43A
Gate To Emitter Voltage (max)
±20V
Package Type
TO-247
Pin Count
3 +Tab
Mounting
Through Hole
Operating Temperature (min)
-55C
Operating Temperature (max)
150C
Operating Temperature Classification
Military
Operating Temperature Range
-55°C To +150°C
Lead Free Status / RoHS Status
Lead free / RoHS Compliant
Available stocks
Company
Part Number
Manufacturer
Quantity
Price
Company:
Part Number:
HGTG11N120CND
Manufacturer:
FSC
Quantity:
5 000
Part Number:
HGTG11N120CND
Manufacturer:
FAIRCHILD/仙童
Quantity:
20 000
©2001 Fairchild Semiconductor Corporation
Test Circuit and Waveforms
Handling Precautions for IGBTs
Insulated Gate Bipolar Transistors are susceptible to
gate-insulation damage by the electrostatic discharge of
energy through the devices. When handling these devices,
care should be exercised to assure that the static charge built
in the handler’s body capacitance is not discharged through
the device. With proper handling and application procedures,
however, IGBTs are currently being extensively used in
production by numerous equipment manufacturers in military,
industrial and consumer applications, with virtually no damage
problems due to electrostatic discharge. IGBTs can be
handled safely if the following basic precautions are taken:
1. Prior to assembly into a circuit, all leads should be kept
2. When devices are removed by hand from their carriers, the
3. Tips of soldering irons should be grounded.
4. Devices should never be inserted into or removed from
5. Gate Voltage Rating - Never exceed the gate-voltage
6. Gate Termination - The gates of these devices are
7. Gate Protection - These devices do not have an internal
shorted together either by the use of metal shorting
springs or by the insertion into conductive material such as
“ECCOSORBD™ LD26” or equivalent.
hand being used should be grounded by any suitable
means - for example, with a metallic wristband.
circuits with power on.
rating of V
permanent damage to the oxide layer in the gate region.
essentially capacitors. Circuits that leave the gate open-
circuited or floating should be avoided. These conditions
can result in turn-on of the device due to voltage buildup on
the input capacitor due to leakage currents or pickup.
monolithic Zener diode from gate to emitter. If gate
protection is required an external Zener is recommended.
FIGURE 20. INDUCTIVE SWITCHING TEST CIRCUIT
R
G
GEM
= 10Ω
. Exceeding the rated V
L = 2mH
HGTG11N120CND
GE
+
-
can result in
V
DD
= 960V
Operating Frequency Information
Operating frequency information for a typical device (Figure 3)
is presented as a guide for estimating device performance for
a specific application. Other typical frequency vs collector
current (I
for a typical unit in Figures 5, 6, 7, 8, 9 and 11. The operating
frequency plot (Figure 3) of a typical device shows f
f
based on measurements of a typical device and is bounded
by the maximum rated junction temperature.
f
Deadtime (the denominator) has been arbitrarily held to 10%
of the on-state time for a 50% duty factor. Other definitions are
possible. t
turn-off delay can establish an additional frequency limiting
condition for an application other than T
important when controlling output ripple under a lightly loaded
condition.
f
allowable dissipation (P
The sum of device switching and conduction losses must not
exceed P
conduction losses (P
P
E
in Figure 21. E
loss (I
instantaneous power loss (I
losses are included in the calculation for E
collector current equals zero (I
MAX2
MAX1
MAX2
V
V
I
CE
C
ON
GE
CE
= (V
and E
CE
; whichever is smaller at each point. The information is
is defined by f
is defined by f
CE
FIGURE 21. SWITCHING TEST WAVEFORMS
CE
D
x V
d(OFF)I
. A 50% duty factor was used (Figure 3) and the
OFF
x I
) plots are possible using the information shown
CE
CE
ON
t
) during turn-on and E
d(OFF)I
are defined in the switching waveforms shown
)/2.
90%
and t
is the integral of the instantaneous power
10%
MAX1
MAX2
C
) are approximated by
d(ON)I
t
D
fI
) is defined by P
= 0.05/(t
= (P
CE
E
are defined in Figure 21. Device
CE
OFF
x V
90%
D
- P
= 0).
CE
d(OFF)I
C
) during turn-off. All tail
OFF
E
)/(E
ON
JM
10%
D
OFF
is the integral of the
OFF
. t
+ t
= (T
t
d(ON)I
HGTG11N120CND Rev. B
d(OFF)I
d(ON)I
+ E
t
; i.e., the
JM
rI
ON
- T
).
MAX1
is
C
). The
)/R
θJC
or
.