FAN4800IN Fairchild Semiconductor, FAN4800IN Datasheet - Page 13
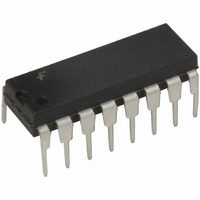
FAN4800IN
Manufacturer Part Number
FAN4800IN
Description
IC PFC CONTROLLER CCM/DCM 16DIP
Manufacturer
Fairchild Semiconductor
Specifications of FAN4800IN
Mode
Continuous Conduction (CCM), Discontinuous Conduction (DCM)
Frequency - Switching
66kHz ~ 84kHz
Current - Startup
100µA
Voltage - Supply
11 V ~ 16.5 V
Operating Temperature
-40°C ~ 125°C
Mounting Type
Through Hole
Package / Case
16-DIP (0.300", 7.62mm)
Mounting Style
Through Hole
Lead Free Status / RoHS Status
Lead free / RoHS Compliant
Available stocks
Company
Part Number
Manufacturer
Quantity
Price
Part Number:
FAN4800IN
Manufacturer:
FSC
Quantity:
20 000
FAN4800 Rev. 1.0.5
© 2005 Fairchild Semiconductor Corporation
1.10 Example
For the application circuit shown in Figures 12 and 13,
with the oscillator running at:
solving for C
R
The dead time of the oscillator adds to the maximum
PWM duty cycle (it is an input to the duty cycle limiter).
With zero oscillator dead time, the maximum PWM duty
cycle is typically 47%. Take care not to make C
large, which could extend the maximum duty cycle
beyond 50%. This can be accomplished by using no
greater than a 390pF capacitor for C
2. PWM Section
2.1 Pulse Width Modulator (PWM)
The operation of the PWM section of the FAN4800 is
straightforward, but there are several points that should
be noted. Foremost among these is the inherent syn-
chronization of PWM with the PFC section of the device,
from which it also derives its basic timing. The PWM is
capable of current-mode or voltage-mode operation. In
current-mode applications, the PWM ramp (RAMP2) is
usually derived directly from a current sensing resistor or
current transformer in the primary of the output stage. it
is thereby representative of the current flowing in the
converter’s output stage. DC I
by-cycle current limiting, is typically connected to
RAMP2 in such applications. For voltage-mode opera-
tion and certain specialized applications, RAMP2 can be
connected to a separate RC timing network to generate
a voltage ramp against which V
these conditions, the use of voltage feed-forward from
the PFC bus can assist in line regulation accuracy and
response. As in current-mode operation, the DC I
input is used for output stage over-current protection.
No voltage error amplifier is included in the PWM stage
of the FAN4800, as this function is generally performed
on the output side of the PWM’s isolation boundary. To
facilitate the design of opto-coupler feedback circuitry, an
offset has been built into the PWM’s RAMP2 input that
allows V
ages below typical 0.9V.
2.2 PWM Current Limit
The DC I
current limiter for the PWM section. Should the input
voltage at this pin ever exceed 1V, the output flip-flop is
reset by the clock pulse at the start of the next PWM
power cycle. When the DC I
T
is 51.1kΩ, selecting standard components values.
DC
LIMIT
to command a 0% duty cycle for input volt-
T
x R
pin is a direct input to the cycle-by-cycle
f
OSC
T
yields 1.96 x 10
=
100kHz
=
LIMIT
LIMIT
t
RAMP
DC
1
, which provides cycle-
triggers the cycle-by-
T
is compared. Under
-4
.
. C
T
is 390pF and
T
LIMIT
(12)
too
13
cycle current, it also softly discharges the voltage of the
soft-start capacitor. It limits the PWM duty cycle mode
and the power dissipation is reduced during the dead-
short condition.
2.3 V
The V
PFC and inhibits the PWM if the voltage on V
than its nominal 2.25V. Once the voltage reaches 2.25V,
which corresponds to the PFC output capacitor being
charged to its rated boost voltage, the soft-start begins.
2.4 PWM Control (RAMP2)
When the PWM section is used in current mode, RAMP2
is generally used as the sampling point for a voltage,
representing the current in the primary of the PWM’s out-
put transformer. The voltage is derived either from a cur-
rent sensing resistor or a current transformer. In voltage
mode, RAMP2 is the input for a ramp voltage generated
by a second set of timing components (R
that have a minimum value of 0V and a peak value of
approximately 5V. In voltage mode, feed forward from
the PFC output bus is an excellent way to derive the tim-
ing ramp for the PWM stage.
2.5 Soft-Start (SS)
PWM start-up is controlled by selection of the external
capacitor at soft-start. A current source of 20mA supplies
the charging current for the capacitor and start-up of the
PWM begins at 0.9V. Start-up delay can be programmed
by the following equation:
where C
t
It is important that the time constant of the PWM soft-
start allows the PFC time to generate sufficient output
power for the PWM section. The PWM start-up delay
should be at least 5ms.
Solving for the minimum value of C
Use caution when using this minimum soft-start capaci-
tance value because it can cause premature charging of
the SS capacitor and activation of the PWM section if
V
at start-up. The magnitude of V
both to line voltage and nominal PFC output voltage.
Typically, a 1.0µF soft-start capacitor allows time for V
and PFC
vation of the PWM section at line voltages between
90Vrms and 265Vrms.
DELAY
FB
is in the hysteresis band of the V
IN
IN
is the desired start-up delay.
OK Comparator
SS
OK comparator monitors the DC output of the
OUT
is the required soft-start capacitance and the
to reach their nominal values prior to acti-
C
SS
=
C
5ms
SS
=
×
t
DELAY
20μA
0.9V
×
=
FB
20μA
111nF
0.9V
SS
at start-up is related
:
IN
RAMP2
OK comparator
www.fairchildsemi.com
, C
FB
RAMP2
is less
(13)
(14)
FB
)