SI1005-C-GM Silicon Laboratories Inc, SI1005-C-GM Datasheet - Page 145
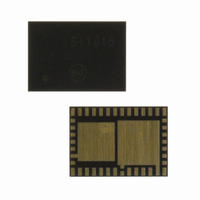
SI1005-C-GM
Manufacturer Part Number
SI1005-C-GM
Description
IC TXRX MCU + EZRADIOPRO
Manufacturer
Silicon Laboratories Inc
Specifications of SI1005-C-GM
Package / Case
42-QFN
Frequency
240MHz ~ 960MHz
Data Rate - Maximum
256kbps
Modulation Or Protocol
FSK, GFSK, OOK
Applications
General Purpose
Power - Output
13dBm
Sensitivity
-121dBm
Voltage - Supply
0.9 V ~ 1.8 V
Current - Receiving
18.5mA
Current - Transmitting
30mA
Data Interface
PCB, Surface Mount
Memory Size
32kB Flash, 4kB RAM
Antenna Connector
PCB, Surface Mount
Number Of Receivers
1
Number Of Transmitters
1
Wireless Frequency
240 MHz to 960 MHz
Interface Type
UART, SMBus, SPI, PCA
Output Power
13 dBm
Operating Supply Voltage
0.9 V to 3.6 V
Maximum Operating Temperature
+ 85 C
Mounting Style
SMD/SMT
Maximum Supply Current
4.1 mA
Minimum Operating Temperature
- 40 C
Modulation
FSK, GFSK, OOK
Protocol Supported
C2, SMBus
Core
8051
Program Memory Type
Flash
Program Memory Size
32 KB
Data Ram Size
4352 B
Supply Current (max)
4.1 mA
Lead Free Status / RoHS Status
Lead free / RoHS Compliant
Operating Temperature
-
Lead Free Status / Rohs Status
Lead free / RoHS Compliant
Other names
336-1875-5
Available stocks
Company
Part Number
Manufacturer
Quantity
Price
Company:
Part Number:
SI1005-C-GM
Manufacturer:
Silicon Labs
Quantity:
135
- Current page: 145 of 376
- Download datasheet (3Mb)
13.4. Determining the Device Part Number at Run Time
In many applications, user software may need to determine the MCU part number at run time in order to
determine the hardware capabilities. The part number can be determined by reading the value of the Flash
byte at address 0xFFFE.
The value of the Flash byte at address 0xFFFE can be decoded as follows:
0xD0—Si1000
0xD1—Si1001
0xD2—Si1002
0xD3—Si1003
13.5. Flash Write and Erase Guidelines
Any system which contains routines which write or erase Flash memory from software involves some risk
that the write or erase routines will execute unintentionally if the CPU is operating outside its specified
operating range of VDD, system clock frequency, or temperature. This accidental execution of Flash modi-
fying code can result in alteration of Flash memory contents causing a system failure that is only recover-
able by re-Flashing the code in the device.
To help prevent the accidental modification of Flash by firmware, the VDD Monitor must be enabled and
enabled as a reset source on C8051F92x-C8051F93x devices for the Flash to be successfully modified. If
either the VDD Monitor or the VDD Monitor reset source is not enabled, a Flash Error Device Reset
will be generated when the firmware attempts to modify the Flash.
The following guidelines are recommended for any system that contains routines which write or erase
Flash from code.
13.5.1. VDD Maintenance and the VDD Monitor
1. If the system power supply is subject to voltage or current "spikes," add sufficient transient protection
2. Make certain that the minimum V
3. Keep the on-chip VDD Monitor enabled and enable the V
Notes: On Si1000/1/2/3/4/5 devices, both the V
4. As an added precaution, explicitly enable the V
devices to the power supply to ensure that the supply voltages listed in the Absolute Maximum Ratings
table are not exceeded.
this rise time specification, then add an external VDD brownout circuit to the RST pin of the device that
holds the device in reset until V
V
as possible. This should be the first set of instructions executed after the Reset Vector. For C-based
systems, this will involve modifying the startup code added by the C compiler. See your compiler
documentation for more details. Make certain that there are no delays in software between enabling the
V
found in “AN201: Writing to Flash from Firmware," available from the Silicon Laboratories website.
source inside the functions that write and erase Flash memory. The V
should be placed just after the instruction to set PSWE to a 1, but before the Flash write or erase
operation instruction.
DD
DD
or erase Flash without generating a Flash Error Device Reset.
On Si1000/1/2/3/4/5 devices, both the V
after a power-on reset.
drops below the minimum device operating voltage.
Monitor and enabling the V
DD
DD
DD
reaches the minimum device operating voltage and re-asserts RST if
Monitor as a reset source. Code examples showing this can be
rise time specification of 1 ms is met. If the system cannot meet
DD
DD
Monitor and the V
Monitor and the V
Rev. 1.0
DD
Monitor and enable the V
DD
DD
DD
Monitor as a reset source as early in code
Monitor reset source are enabled by hardware
Monitor reset source must be enabled to write
Si1000/1/2/3/4/5
DD
Monitor enable instructions
DD
Monitor as a reset
145
Related parts for SI1005-C-GM
Image
Part Number
Description
Manufacturer
Datasheet
Request
R

Part Number:
Description:
SMD/C°/SINGLE-ENDED OUTPUT SILICON OSCILLATOR
Manufacturer:
Silicon Laboratories Inc

Part Number:
Description:
Manufacturer:
Silicon Laboratories Inc
Datasheet:

Part Number:
Description:
N/A N/A/SI4010 AES KEYFOB DEMO WITH LCD RX
Manufacturer:
Silicon Laboratories Inc
Datasheet:

Part Number:
Description:
N/A N/A/SI4010 SIMPLIFIED KEY FOB DEMO WITH LED RX
Manufacturer:
Silicon Laboratories Inc
Datasheet:

Part Number:
Description:
N/A/-40 TO 85 OC/EZLINK MODULE; F930/4432 HIGH BAND (REV E/B1)
Manufacturer:
Silicon Laboratories Inc

Part Number:
Description:
EZLink Module; F930/4432 Low Band (rev e/B1)
Manufacturer:
Silicon Laboratories Inc

Part Number:
Description:
I°/4460 10 DBM RADIO TEST CARD 434 MHZ
Manufacturer:
Silicon Laboratories Inc

Part Number:
Description:
I°/4461 14 DBM RADIO TEST CARD 868 MHZ
Manufacturer:
Silicon Laboratories Inc

Part Number:
Description:
I°/4463 20 DBM RFSWITCH RADIO TEST CARD 460 MHZ
Manufacturer:
Silicon Laboratories Inc

Part Number:
Description:
I°/4463 20 DBM RADIO TEST CARD 868 MHZ
Manufacturer:
Silicon Laboratories Inc

Part Number:
Description:
I°/4463 27 DBM RADIO TEST CARD 868 MHZ
Manufacturer:
Silicon Laboratories Inc

Part Number:
Description:
I°/4463 SKYWORKS 30 DBM RADIO TEST CARD 915 MHZ
Manufacturer:
Silicon Laboratories Inc

Part Number:
Description:
N/A N/A/-40 TO 85 OC/4463 RFMD 30 DBM RADIO TEST CARD 915 MHZ
Manufacturer:
Silicon Laboratories Inc

Part Number:
Description:
I°/4463 20 DBM RADIO TEST CARD 169 MHZ
Manufacturer:
Silicon Laboratories Inc