ISL6567CRZ Intersil, ISL6567CRZ Datasheet - Page 24
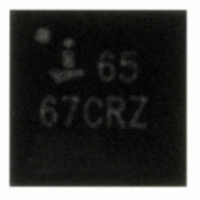
ISL6567CRZ
Manufacturer Part Number
ISL6567CRZ
Description
IC CTLR PWM 2PHASE BUCK 24-QFN
Manufacturer
Intersil
Datasheet
1.ISL6567CRZ.pdf
(26 pages)
Specifications of ISL6567CRZ
Pwm Type
Voltage Mode
Number Of Outputs
1
Frequency - Max
1.5MHz
Duty Cycle
66%
Voltage - Supply
4.9 V ~ 5.5 V
Buck
Yes
Boost
No
Flyback
No
Inverting
No
Doubler
No
Divider
No
Cuk
No
Isolated
No
Operating Temperature
0°C ~ 70°C
Package / Case
24-VQFN
Frequency-max
1.5MHz
Rohs Compliant
YES
Lead Free Status / RoHS Status
Lead free / RoHS Compliant
Available stocks
Company
Part Number
Manufacturer
Quantity
Price
Company:
Part Number:
ISL6567CRZ
Manufacturer:
Intersil
Quantity:
620
Company:
Part Number:
ISL6567CRZ
Manufacturer:
INTERSIL
Quantity:
8 831
Part Number:
ISL6567CRZ
Manufacturer:
INTERSIL
Quantity:
20 000
Part Number:
ISL6567CRZ-T
Manufacturer:
INTERSIL
Quantity:
20 000
Lastly, the conduction loss part of the upper MOSFET’s
power dissipation, P
Equation 30.
In this case, of course, r
upper MOSFET.
The total power dissipated by the upper MOSFET at full load
can be approximated as the summation of these results.
Since the power equations depend on MOSFET parameters,
choosing the correct MOSFETs can be an iterative process
that involves repetitively solving the loss equations for
different MOSFETs and different switching frequencies until
converging upon the best solution.
OUTPUT CAPACITOR SELECTION
The output capacitor is selected to meet both the dynamic
load requirements and the voltage ripple requirements. The
load transient a microprocessor impresses is characterized
by high slew rate (di/dt) current demands. In general,
multiple high quality capacitors of different size and dielectric
are paralleled to meet the design constraints.
Should the load be characterized by high slew rates, attention
should be particularly paid to the selection and placement of
high-frequency decoupling capacitors (MLCCs, typically
multi-layer ceramic capacitors). High frequency capacitors
supply the initially transient current and slow the load
rate-of-change seen by the bulk capacitors. The bulk filter
capacitor values are generally determined by the ESR
(effective series resistance) and capacitance requirements.
High frequency decoupling capacitors should be placed as
close to the power pins of the load, or for that reason, to any
decoupling target they are meant for, as physically possible.
Attention should be paid as not to add inductance in the
circuit board wiring that could cancel the usefulness of these
low inductance components. Consult with the manufacturer
of the load on specific decoupling requirements.
Use only specialized low-ESR capacitors intended for
switching-regulator applications for the bulk capacitors. The
bulk capacitor’s ESR determines the output ripple voltage
and the initial voltage drop following a high slew-rate
transient’s edge. In most cases, multiple capacitors of small
case size perform better than a single large case capacitor.
Bulk capacitor choices include aluminum electrolytic, OS-Con,
Tantalum and even ceramic dielectrics. An aluminum
electrolytic capacitor’s ESR value is related to the case size
with lower ESR available in larger case sizes. However, the
equivalent series inductance (ESL) of these capacitors
increases with case size and can reduce the usefulness of the
capacitor to high slew-rate transient loading. Unfortunately,
ESL is not a specified parameter. Consult the capacitor
P
UMOS 4 ,
=
r
DS ON
(
)
UMOS,4,
⎛
⎜
⎝
I
-------------
OUT
N
DS(ON)
⎞
⎟
⎠
2
d
24
can be calculated using
+
I
--------- -
is the ON resistance of the
PP
12
2
(EQ. 30)
ISL6567
manufacturer and/or measure the capacitor’s impedance with
frequency to help select a suitable component.
OUTPUT INDUCTOR SELECTION
One of the parameters limiting the converter’s response to a
load transient is the time required to change the inductor
current. In a multi-phase converter, small inductors reduce
the response time with less impact to the total output ripple
current (as compared to single-phase converters).
The output inductor of each power channel controls the
ripple current. The control IC is stable for channel ripple
current (peak-to-peak) up to twice the average current. A
single channel’s ripple current is approximated by:
The current from multiple channels tend to cancel each other
and reduce the total ripple current. The total output ripple
current can be determined using the curve in Figure 27; it
provides the total ripple current as a function of duty cycle
and number of active channels, normalized to the parameter
K
where L is the channel inductor value.
Find the intersection of the active channel curve and duty
cycle for your particular application. The resulting ripple
current multiplier from the y-axis is then multiplied by the
normalization factor, K
ripple current for the given application.
I
Δ
K
L PP
NORM
I
,
NORM
TOTAL
1.0
0.8
0.6
0.4
0.2
=
0
FIGURE 27. RIPPLE CURRENT vs DUTY CYCLE
at zero duty cycle.
0
V
------------------------------- -
=
=
IN
F
------------------- -
L F
K
SW
V
–
⋅
NORM
OUT
V
⋅
SW
OUT
L
0.1
⋅
×
K
V
--------------- -
CM
V
NORM
OUT
IN
DUTY CYCLE (V
0.2
, to determine the total output
0.3
O
/V
IN
)
0.4
May 28, 2009
(EQ. 33)
(EQ. 32)
(EQ. 31)
FN9243.3
0.5