R88A-CNG01R Omron, R88A-CNG01R Datasheet - Page 365
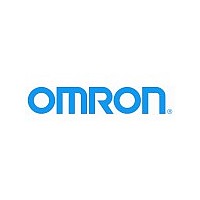
R88A-CNG01R
Manufacturer Part Number
R88A-CNG01R
Description
Encoder Connector ABS Motor
Manufacturer
Omron
Datasheet
1.R88A-CNG01R.pdf
(508 pages)
Specifications of R88A-CNG01R
Lead Free Status / Rohs Status
Lead free / RoHS Compliant
- Current page: 365 of 508
- Download datasheet (22Mb)
Setting range
Setting range
Setting range
Speed and Torque Control Parameters (Pn50 and Higher)
Pn50
Pn51
Pn52
Explanation of Settings
• Use this parameter to set the relation between the voltage applied to the Speed Command Input
• Refer to 5-2 Speed Control on page 5-3 for information on speed control.
• Refer to 5-4 Torque Control on page 5-8 for information on torque control.
• Use this parameter to reverse the polarity of the Speed Command Input (REF: CN1 pin 14) to
• This parameter is set to 0 by default (
• This parameter is disabled if the Zero Speed Designation/Speed Command Direction Switch
• The operation of the Servomotor may be abnormal if the polarity of the speed command signal
• Use this parameter to adjust the offset of the Speed Command Input (REF: CN1 pin 14).
• The offset amount is approximately the set value times 0.3 mV.
• There are two ways to adjust the offset.
• The manual adjustment is as follows:
• The automatic adjustment is as follows:
(REF: CN1 pin 14) and the Servomotor speed.
change the Servomotor rotation direction without reversing the polarity of the commands from the
host controller.
compatibility with all OMNUC W-Series Servo Drives.
(Pn06) is set to 2.
from the Position Control Unit does not agree with the setting of this parameter when the Servo
Drive is in Speed Control Mode and the Servo Drive is used in combination with an external
Position Control Unit.
• Manually
• Automatically
• To adjust the offset for individual Servo Drives, accurately input 0 V to the Speed/Torque
• If you use a position loop in the host controller, set this parameter so that there are no
• This parameter will be automatically set when automatic offset adjustment is executed. Refer to
Command Speed Rotation Direction Switch
Speed Command Scale
Speed Command Offset Adjustment
Command Input (REF/TREF1) (or connect REF/TREF1 to the signal ground), and then set this
parameter so that the Servomotor does not rotate.
accumulated pulses at servo lock status.
Automatic Offset Adjustment on page 6-22 for the procedure.
Setting
0
1
−2047 to 2047
10 to 2000
0 or 1
Direction of motor rotation:
Clockwise (forward) for positive commands when viewing the end of the shaft
Direction of motor rotation:
Counterclockwise (reverse) for positive commands when viewing the end of the shaft
Unit
Unit
Unit
(r/min)/V
0.3 mV
counterclockwise (reverse) for positive commands
---
Explanation
Default setting
Default setting
Default setting
5-16 User Parameters
300
0
0
Power OFF→ON
Power OFF→ON
Power OFF→ON
Speed Torque
Speed Torque
) for
Speed
5-80
---
---
---
5
Related parts for R88A-CNG01R
Image
Part Number
Description
Manufacturer
Datasheet
Request
R

Part Number:
Description:
G6S-2GLow Signal Relay
Manufacturer:
Omron Corporation
Datasheet:

Part Number:
Description:
Compact, Low-cost, SSR Switching 5 to 20 A
Manufacturer:
Omron Corporation
Datasheet:

Part Number:
Description:
Manufacturer:
Omron Corporation
Datasheet:

Part Number:
Description:
Manufacturer:
Omron Corporation
Datasheet:

Part Number:
Description:
Manufacturer:
Omron Corporation
Datasheet:

Part Number:
Description:
Manufacturer:
Omron Corporation
Datasheet:

Part Number:
Description:
Manufacturer:
Omron Corporation
Datasheet:

Part Number:
Description:
Manufacturer:
Omron Corporation
Datasheet: