122-28176 Parallax Inc, 122-28176 Datasheet - Page 234
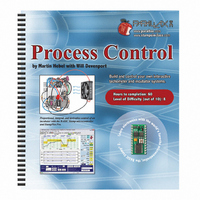
122-28176
Manufacturer Part Number
122-28176
Description
GUIDE STUDENT PROCESS CONTROL
Manufacturer
Parallax Inc
Specifications of 122-28176
Accessory Type
Manual
Product
Microcontroller Accessories
Lead Free Status / RoHS Status
Contains lead / RoHS non-compliant
For Use With/related Products
Propeller Education (PE) Kit
Lead Free Status / RoHS Status
Lead free / RoHS Compliant, Contains lead / RoHS non-compliant
- Current page: 234 of 330
- Download datasheet (11Mb)
Page 224 · Process Control
We will use the same circuitry to overview and apply proportional, integral, and
derivative control modes. Figure 7-2 (identical to Figure 6-17) is a schematic of the
circuitry necessary for the next two exercises. The test tube provides the environment we
wish to control. The heater drive provides full power for developing heat in the resistor.
Let’s assume it is our objective to maintain temperature within the test tube at 101.50 °F
within 1 degree. This would be representative of the requirements of an incubator used
for hatching eggs. Maintaining the eggs at the setpoint temperature of 101.5 °F is perfect,
but the temperature could go up to 102.50 °F or down to 100.50 °F without damage to the
embryos. Although it may be hard to imagine an incubator when you look at your test
tube, the BASIC Stamp would be well suited as the controller in a large commercial
hatchery incubator.
To maintain temperature at the desired value seems like a pretty “common sense” task.
That is, simply measure temperature; if it is above the setpoint, turn the heater OFF; and,
if it is below, turn the heater ON. The simplest kind of control mode is on-off control.
There are drawbacks to this control mode, however. During the following exercise, you
will establish on-off control of your model incubator. Pay close attention to the
characteristics exhibited by your model. These characteristics would also apply to real
control applications.
Programming for this application requires data acquisition, evaluation, and control action.
Our display routine will also include storing and displaying the minimum and maximum
overshoot in the process. The structure and much of the content of prior programs will
be used to acquire and calculate our measurement. Instead of turning the heater on
continually, a new subroutine will be added to evaluate and control it. Evaluation will be
based on a setpoint variable. Figure 7-3 is a partial flowchart of the control action.
Related parts for 122-28176
Image
Part Number
Description
Manufacturer
Datasheet
Request
R

Part Number:
Description:
MANUAL FOR SUMOBOT
Manufacturer:
Parallax Inc
Datasheet:

Part Number:
Description:
GUIDE STUDENT SMART SENSORS
Manufacturer:
Parallax Inc
Datasheet:

Part Number:
Description:
MANUAL PROPELLER
Manufacturer:
Parallax Inc
Datasheet:

Part Number:
Description:
LEAD WIRES FLYING CABLE III/IV
Manufacturer:
Xilinx Inc
Datasheet:

Part Number:
Description:
BOARD ADAPTER AND FLY LEADS
Manufacturer:
Xilinx Inc
Datasheet:

Part Number:
Description:
PLATFORM CABLE USB II
Manufacturer:
Xilinx Inc
Datasheet:

Part Number:
Description:
KIT STARTER COOLRUNNER-II BUNDLE
Manufacturer:
Xilinx Inc
Datasheet:

Part Number:
Description:
Microcontroller Modules & Accessories DISCONTINUED BY PARALLAX
Manufacturer:
Parallax Inc

Part Number:
Description:
Microcontroller Modules & Accessories DISCONTINUED BY PARALLAX
Manufacturer:
Parallax Inc

Part Number:
Description:
BOOK UNDERSTANDING SIGNALS
Manufacturer:
Parallax Inc
Datasheet:

Part Number:
Description:
BOARD EXPERIMENT+LCD NX-1000
Manufacturer:
Parallax Inc
Datasheet:

Part Number:
Description:
IC MCU 2K FLASH 50MHZ SO-18
Manufacturer:
Parallax Inc
Datasheet: