122-28176 Parallax Inc, 122-28176 Datasheet - Page 257
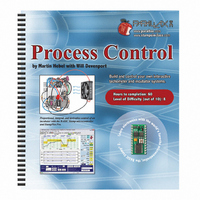
122-28176
Manufacturer Part Number
122-28176
Description
GUIDE STUDENT PROCESS CONTROL
Manufacturer
Parallax Inc
Specifications of 122-28176
Accessory Type
Manual
Product
Microcontroller Accessories
Lead Free Status / RoHS Status
Contains lead / RoHS non-compliant
For Use With/related Products
Propeller Education (PE) Kit
Lead Free Status / RoHS Status
Lead free / RoHS Compliant, Contains lead / RoHS non-compliant
- Current page: 257 of 330
- Download datasheet (11Mb)
Chapter 8: Proportional-Integral-Derivative Control · Page 247
be to only change the pedal position a small amount.
Your control reaction is
proportional to the absolute magnitude of the mph error.
Next, consider that your car is going up a long continuous hill and your speed drops to 45
mph. At 10 mph below your desired setpoint, the proportional reaction above was
enough to overcome some of the effects of the incline but, due to the long hill, your car
stabilizes at 50 mph. What would you do? Understanding your objective is to go 55
mph, you would naturally press down a little harder. And, if that brought the speed up to
52 mph, would you stop pressing? No, you would press a little more and a little more
until finally you had integrated exactly enough control action to compensate for the
steepness of the hill and be at 55 mph. As a smart controller, you would not allow long-
term continuous error to persist in your process.
Finally, consider how you might react to driving up a steep hill versus the last long
continuous hill. Remember that in our example you are reacting to what you see the
speedometer doing – it is providing you process feedback information. If all of a sudden
you notice your speed is dropping quickly, what do you assume? Right, you have just
gotten onto a very steep hill. What will happen if you do not respond quickly and
forcefully to this rapid change in your speed? Things may only get worse, right? Having
an element of control in which you respond relative to the rate at which your process is
changing can help buffer the affects of rapidly occurring, high magnitude disturbances.
Responding to the rate of change at which an error is occurring is the function of
derivative control. When you work with derivatives in mathematics you are usually
analyzing the slope at points along a changing curve. Derivative control action responds
solely to the slope of the error, or the speed at which the value is changing.
Hopefully, as you think of yourself as an intelligent PID controller in our driving
example, you can see how a blended response to the absolute magnitude of error (P), the
duration that an error persists (I), and the rate that error is occurring (D) can provide very
efficient and effective process control.
Determining the appropriate blend of the
individual control modes must take into account the dynamics of the entire system. As
with all continuous process control scenarios, keeping your car at a steady speed is
dynamic.
There is a dynamic to the magnitude, duration, and rate at which road
conditions change. The time required for individual drivers to notice, evaluate, and react
to speedometer changes is dynamic. And, the weight, engine torque, and transmission
ratio are only a few of the dynamic variables of your car that defines its response to a
throttle change. As a “smart controller” behind the wheel you will find yourself quickly
adapting the blend of your PID response based on the characteristics of your vehicle as
Related parts for 122-28176
Image
Part Number
Description
Manufacturer
Datasheet
Request
R

Part Number:
Description:
MANUAL FOR SUMOBOT
Manufacturer:
Parallax Inc
Datasheet:

Part Number:
Description:
GUIDE STUDENT SMART SENSORS
Manufacturer:
Parallax Inc
Datasheet:

Part Number:
Description:
MANUAL PROPELLER
Manufacturer:
Parallax Inc
Datasheet:

Part Number:
Description:
LEAD WIRES FLYING CABLE III/IV
Manufacturer:
Xilinx Inc
Datasheet:

Part Number:
Description:
BOARD ADAPTER AND FLY LEADS
Manufacturer:
Xilinx Inc
Datasheet:

Part Number:
Description:
PLATFORM CABLE USB II
Manufacturer:
Xilinx Inc
Datasheet:

Part Number:
Description:
KIT STARTER COOLRUNNER-II BUNDLE
Manufacturer:
Xilinx Inc
Datasheet:

Part Number:
Description:
Microcontroller Modules & Accessories DISCONTINUED BY PARALLAX
Manufacturer:
Parallax Inc

Part Number:
Description:
Microcontroller Modules & Accessories DISCONTINUED BY PARALLAX
Manufacturer:
Parallax Inc

Part Number:
Description:
BOOK UNDERSTANDING SIGNALS
Manufacturer:
Parallax Inc
Datasheet:

Part Number:
Description:
BOARD EXPERIMENT+LCD NX-1000
Manufacturer:
Parallax Inc
Datasheet:

Part Number:
Description:
IC MCU 2K FLASH 50MHZ SO-18
Manufacturer:
Parallax Inc
Datasheet: