122-28176 Parallax Inc, 122-28176 Datasheet - Page 306
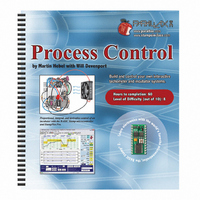
122-28176
Manufacturer Part Number
122-28176
Description
GUIDE STUDENT PROCESS CONTROL
Manufacturer
Parallax Inc
Specifications of 122-28176
Accessory Type
Manual
Product
Microcontroller Accessories
Lead Free Status / RoHS Status
Contains lead / RoHS non-compliant
For Use With/related Products
Propeller Education (PE) Kit
Lead Free Status / RoHS Status
Lead free / RoHS Compliant, Contains lead / RoHS non-compliant
- Current page: 306 of 330
- Download datasheet (11Mb)
Note the response of %Dd:
Derivative control drives to oppose the rising or falling temperature. When K
changed to 10, a small change in error produces very large changes in drive. The
response of the system is such that there were almost no oscillations. With Proportional-
Derivative control, a high proportional gain will assist control of the system by having a
fast response, and results in very little proportional error. With derivative control, the
heavy oscillations associated with a high proportional gain can be damped, resulting in a
very fast, stable response. But too much derivative gain can lead to very unstable control
of the system. Around time 24, the gain was increased to 50. With just a little
disturbance, the erratic behavior of the system can be seen. As proportional drive tried to
raise the temperature to the setpoint, derivate control fought any upwards motion. The
total drive cycled continually between 0% and 100% as the error went one way and then
the other. If this were an oil-flow system, consider what the pump must sound like
during this control!
Derivative can be very good for limiting the effect of an error. Imagine operating at the
setpoint, and quick, short disturbance causes the temperature to drop suddenly.
Derivative drive will rapidly increase the output to limit the amount of the temperature
drop. We were not able to show this response well with our slow-responding system.
Can you?
Challenge 8-6: Derivative Control Testing
Can a system be controlled on derivative drive alone?
•
•
•
√
√
√
√
√
Temperature increasing → %Dd is negative.
Temperature decreasing → %Dd is positive.
Temperature constant → %Dd is 0.
After establishing operation near the setpoint, set Kp, Ki to 0 and %Bias to 0.
Set Kd to a value of your choosing.
Provide a cooling disturbance and test control of the system.
Allow operation for several minutes.
Discuss the results of your testing.
P
is
Related parts for 122-28176
Image
Part Number
Description
Manufacturer
Datasheet
Request
R

Part Number:
Description:
MANUAL FOR SUMOBOT
Manufacturer:
Parallax Inc
Datasheet:

Part Number:
Description:
GUIDE STUDENT SMART SENSORS
Manufacturer:
Parallax Inc
Datasheet:

Part Number:
Description:
MANUAL PROPELLER
Manufacturer:
Parallax Inc
Datasheet:

Part Number:
Description:
LEAD WIRES FLYING CABLE III/IV
Manufacturer:
Xilinx Inc
Datasheet:

Part Number:
Description:
BOARD ADAPTER AND FLY LEADS
Manufacturer:
Xilinx Inc
Datasheet:

Part Number:
Description:
PLATFORM CABLE USB II
Manufacturer:
Xilinx Inc
Datasheet:

Part Number:
Description:
KIT STARTER COOLRUNNER-II BUNDLE
Manufacturer:
Xilinx Inc
Datasheet:

Part Number:
Description:
Microcontroller Modules & Accessories DISCONTINUED BY PARALLAX
Manufacturer:
Parallax Inc

Part Number:
Description:
Microcontroller Modules & Accessories DISCONTINUED BY PARALLAX
Manufacturer:
Parallax Inc

Part Number:
Description:
BOOK UNDERSTANDING SIGNALS
Manufacturer:
Parallax Inc
Datasheet:

Part Number:
Description:
BOARD EXPERIMENT+LCD NX-1000
Manufacturer:
Parallax Inc
Datasheet:

Part Number:
Description:
IC MCU 2K FLASH 50MHZ SO-18
Manufacturer:
Parallax Inc
Datasheet: