122-28176 Parallax Inc, 122-28176 Datasheet - Page 260
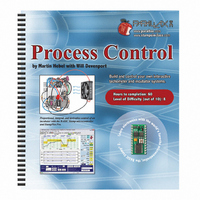
122-28176
Manufacturer Part Number
122-28176
Description
GUIDE STUDENT PROCESS CONTROL
Manufacturer
Parallax Inc
Specifications of 122-28176
Accessory Type
Manual
Product
Microcontroller Accessories
Lead Free Status / RoHS Status
Contains lead / RoHS non-compliant
For Use With/related Products
Propeller Education (PE) Kit
Lead Free Status / RoHS Status
Lead free / RoHS Compliant, Contains lead / RoHS non-compliant
- Current page: 260 of 330
- Download datasheet (11Mb)
With each element in PID, the control action is based on the error, either current,
accumulated over time, or change with respect to time. Mathematically, integrals and
derivatives are based on an infinite number of points in the time continuum. Consider
Figure 8-2 showing an actual reading oscillating around a setpoint. Data is measured and
action taken at every possible point. The integral evaluation provides the area under the
curve. As an example, if the error resulted in a certain amount of power being expended,
the integral of the error would provide the total power used over time. The mathematical
result would provide a very precise value for the area under the curve. Note that if a
value above the setpoint were considered a positive error, data below the setpoint would
be a negative error. If the areas A and B were equal and these two areas were integrated,
the result would be 0.
•
•
•
•
Error (E) is the measurement from the desired setpoint to the actual system
condition, such as a difference between the desired temperature and the actual
temperature.
Proportional Drive continuously evaluates error and adds or subtracts output
drive in an attempt to drive the system back to the setpoint. Too low? More
drive. Too high? Less drive. The gain is used to adjust how much action is
taken based on the error.
Integral Drive measures the duration and magnitude of the error and adds or
subtracts to eliminate the long lasting error. The longer the error and the greater
the amount of error, the greater the integral drive will be. Gain is used to adjust
the amount of action based on the duration and magnitude of error.
Derivative Drive measures how quickly error changes in respect to time. The
faster the error changes, the more action that will be taken to oppose the change
to bring the system back under control. The gain once again is used to adjust the
amount of action based on this calculation.
Figure 8-2
Continuous
Measurement for
PID
Related parts for 122-28176
Image
Part Number
Description
Manufacturer
Datasheet
Request
R

Part Number:
Description:
MANUAL FOR SUMOBOT
Manufacturer:
Parallax Inc
Datasheet:

Part Number:
Description:
GUIDE STUDENT SMART SENSORS
Manufacturer:
Parallax Inc
Datasheet:

Part Number:
Description:
MANUAL PROPELLER
Manufacturer:
Parallax Inc
Datasheet:

Part Number:
Description:
LEAD WIRES FLYING CABLE III/IV
Manufacturer:
Xilinx Inc
Datasheet:

Part Number:
Description:
BOARD ADAPTER AND FLY LEADS
Manufacturer:
Xilinx Inc
Datasheet:

Part Number:
Description:
PLATFORM CABLE USB II
Manufacturer:
Xilinx Inc
Datasheet:

Part Number:
Description:
KIT STARTER COOLRUNNER-II BUNDLE
Manufacturer:
Xilinx Inc
Datasheet:

Part Number:
Description:
Microcontroller Modules & Accessories DISCONTINUED BY PARALLAX
Manufacturer:
Parallax Inc

Part Number:
Description:
Microcontroller Modules & Accessories DISCONTINUED BY PARALLAX
Manufacturer:
Parallax Inc

Part Number:
Description:
BOOK UNDERSTANDING SIGNALS
Manufacturer:
Parallax Inc
Datasheet:

Part Number:
Description:
BOARD EXPERIMENT+LCD NX-1000
Manufacturer:
Parallax Inc
Datasheet:

Part Number:
Description:
IC MCU 2K FLASH 50MHZ SO-18
Manufacturer:
Parallax Inc
Datasheet: