122-28176 Parallax Inc, 122-28176 Datasheet - Page 303
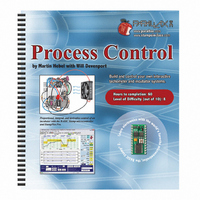
122-28176
Manufacturer Part Number
122-28176
Description
GUIDE STUDENT PROCESS CONTROL
Manufacturer
Parallax Inc
Specifications of 122-28176
Accessory Type
Manual
Product
Microcontroller Accessories
Lead Free Status / RoHS Status
Contains lead / RoHS non-compliant
For Use With/related Products
Propeller Education (PE) Kit
Lead Free Status / RoHS Status
Lead free / RoHS Compliant, Contains lead / RoHS non-compliant
- Current page: 303 of 330
- Download datasheet (11Mb)
Chapter 8: Proportional-Integral-Derivative Control · Page 293
are adding sufficient drive to be at setpoint, the error is nearly 0, therefore proportional
drive is nearly 0. Also at T3, the setpoint is changed to the 50% drive temperature, which
in our case was 96 °F. The drive built up by integral drive must again be removed based
on the error and time.
At T4, the temperature is nearing the setpoint as integral is reduced. Integral drive is
nearly 0 (0.8%), and total drive is 49.1%, with a small error providing –1.7% for
proportional. The setpoint is returned to 105 °F with a K
of 0.005, five times larger than
I
previously. The integral drive builds quickly to cause an overshoot. Integral must again
be reduced by error to bring temperature back down and causing undershoot. Hunting
can occur with integral control, and the durations will be much longer based on the slow
integration times.
At T5, note that the temperature is crossing the setpoint. What happens with the integral
drive at this time? It is at this point that it turns and begins to be reduced. Depending on
how long, and what magnitude of error, integral drive values can become very large.
Integral drive can be thought of as a dynamic bias. Based on error, integral drive will
adjust to get the steady-state controlled variable to the setpoint. When integral drive has
very low gain, the change in %Drive
will be very small, allowing proportional drive to
INT
respond to correct temperature. Large values of K
are usually undesirable as they can
I
cause the controlled output to be driven faster than the system can respond, leading to
high overshoot and oscillations.
It is also important to limit the maximum value that ΣE∆t reaches. A long lasting
disturbance, such as a leaving the incubator door open overnight, could cause the value to
reach extremely high values. Once the door is closed, the drive will be excessive, based
on the high integral drive, and will require a very long time for the positive error to be
driven away. This will lead to very high temperatures for a very long time. This is effect
is called "Integral Windup." Feel free to try this test by removing the cover from the
incubator, and allowing it run for 5 minutes, then replace the cover.
Challenge 8-5: Integral Control Testing
Can a system be controlled using integral control alone? Set %Bias to 50% and Kp to 0
and test the control action, and then discuss the results.
Related parts for 122-28176
Image
Part Number
Description
Manufacturer
Datasheet
Request
R

Part Number:
Description:
MANUAL FOR SUMOBOT
Manufacturer:
Parallax Inc
Datasheet:

Part Number:
Description:
GUIDE STUDENT SMART SENSORS
Manufacturer:
Parallax Inc
Datasheet:

Part Number:
Description:
MANUAL PROPELLER
Manufacturer:
Parallax Inc
Datasheet:

Part Number:
Description:
LEAD WIRES FLYING CABLE III/IV
Manufacturer:
Xilinx Inc
Datasheet:

Part Number:
Description:
BOARD ADAPTER AND FLY LEADS
Manufacturer:
Xilinx Inc
Datasheet:

Part Number:
Description:
PLATFORM CABLE USB II
Manufacturer:
Xilinx Inc
Datasheet:

Part Number:
Description:
KIT STARTER COOLRUNNER-II BUNDLE
Manufacturer:
Xilinx Inc
Datasheet:

Part Number:
Description:
Microcontroller Modules & Accessories DISCONTINUED BY PARALLAX
Manufacturer:
Parallax Inc

Part Number:
Description:
Microcontroller Modules & Accessories DISCONTINUED BY PARALLAX
Manufacturer:
Parallax Inc

Part Number:
Description:
BOOK UNDERSTANDING SIGNALS
Manufacturer:
Parallax Inc
Datasheet:

Part Number:
Description:
BOARD EXPERIMENT+LCD NX-1000
Manufacturer:
Parallax Inc
Datasheet:

Part Number:
Description:
IC MCU 2K FLASH 50MHZ SO-18
Manufacturer:
Parallax Inc
Datasheet: