CJ1W-NC414 Omron, CJ1W-NC414 Datasheet - Page 541
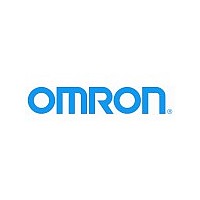
CJ1W-NC414
Manufacturer Part Number
CJ1W-NC414
Description
High Speed Pulse Train 4 Axes
Manufacturer
Omron
Datasheet
1.CJ1W-NC214.pdf
(601 pages)
Specifications of CJ1W-NC414
Lead Free Status / Rohs Status
Lead free / RoHS Compliant
- Current page: 541 of 601
- Download datasheet (14Mb)
CJ Position Control Units OPERATION MANUAL (CJ1W-NC214/234/414/434)
Category
Each
task
Each
axis
Memory Operation
Error
Memory Operation
Condition Data
Error
Forward Direction
Limit Error
Reverse Direction
Limit Error
Emergency Stop
Input
Drive Alarm Input
External Power
Supply Error
Duplicate Start
During Servo
Unlock
Item name
500F
6000
Error code
2XXX
30XX
5008
5009
500D
5100
6001
The setting of memory
operation data is not correct.
The last 3 digits of the error
code indicate the sequence
number under which the
error occurred.
The setting of memory
operation condition data is
not correct. The last 2 digits
of the error code indicate the
condition number under
which the error occurred.
A forward direction limit
signal was input.
A reverse direction limit
signal was input.
An emergency stop signal
was input.
A drive alarm input signal
was input.
The pulse I/O power supply
is not supplied.
Multiple functions that
cannot be executed
simultaneously were
executed on the same axis.
An axis operation command
was executed while the
servo was unlocked.
Cause
Check the setting of the memory
operation data for the applicable
sequence number, and then execute an
error reset.
If this error occurs, the PCU decelerates
all configuration axes of the applicable
task to a stop.
Check the setting of the memory
operation condition data for the
applicable condition number, and then
execute an error reset.
If this error occurs, the PCU decelerates
all configuration axes of the applicable
task to a stop.
Execute an error reset and then perform
recovery operation in the reverse
direction. If a normal state cannot be
recovered, check the connection of the
forward direction limit signal and setting
of the forward direction limit input logic.
If this error occurs, the PCU stops the
applicable axis according to the setting
of the corresponding axis parameter.
Execute an error reset and then perform
recovery operation in the forward
direction. If a normal state cannot be
recovered, check the connection of the
reverse direction limit signal and setting
of the reverse direction limit input logic.
If this error occurs, the PCU stops the
applicable axis according to the setting
of the corresponding axis parameter.
Cancel the emergency stop input and
then execute an error reset. If the error
cannot be reset, check the connection of
the emergency stop signal and setting of
the emergency stop input logic.
If this error occurs, the PCU stops the
applicable axis according to the setting
of the corresponding axis parameter.
Remove the cause of the drive error and
then execute an error reset.
If this error occurs, the PCU stops the
applicable axis according to the setting
of the corresponding axis parameter.
Confirm that the pulse I/O power supply
is supplied, and then execute an error
reset.
If this error occurs, the PCU immediately
stops all axes and switches to the servo
unlocked state.
Check the execution conditions and then
execute an error reset.
If this error occurs, the PCU decelerates
the applicable axis to a stop.
Execute an error reset, and issue the
axis operation command after the servo
is locked.
Release method
12-6 Error Code List
12-32
12
Related parts for CJ1W-NC414
Image
Part Number
Description
Manufacturer
Datasheet
Request
R

Part Number:
Description:
ANALOG IN, CJ1, 4CH, HIGH SPPE
Manufacturer:
Omron
Datasheet:

Part Number:
Description:
High Speed Pulse Train 2 Axes
Manufacturer:
Omron
Datasheet:

Part Number:
Description:
High Speed Pulse Train 2 Axes
Manufacturer:
Omron
Datasheet:

Part Number:
Description:
High Speed Pulse Train 4 Axes
Manufacturer:
Omron
Datasheet:

Part Number:
Description:
CJ Profinet Master
Manufacturer:
Omron
Datasheet:

Part Number:
Description:
Ethernet I/P Module
Manufacturer:
Omron
Datasheet:

Part Number:
Description:
HIGH SPEED COUNTER 500Khz 2 CH
Manufacturer:
Omron
Datasheet:

Part Number:
Description:
Isolated Universal Analog 4pt
Manufacturer:
Omron
Datasheet:

Part Number:
Description:
CJ1 CompoNet Master
Manufacturer:
Omron
Datasheet:

Part Number:
Description:
G6S-2GLow Signal Relay
Manufacturer:
Omron Corporation
Datasheet:

Part Number:
Description:
Compact, Low-cost, SSR Switching 5 to 20 A
Manufacturer:
Omron Corporation
Datasheet:

Part Number:
Description:
Manufacturer:
Omron Corporation
Datasheet: