R88M-W75030T-S1 Omron, R88M-W75030T-S1 Datasheet
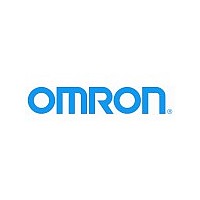
R88M-W75030T-S1
Specifications of R88M-W75030T-S1
Related parts for R88M-W75030T-S1
R88M-W75030T-S1 Summary of contents
Page 1
... Cat. No. I544-E1-05 WITH BUILT-IN MECHATROLINK-II COMMUNICATIONS USER’S MANUAL OMNUC W AC SERVOMOTORS/SERVO DRIVERS SERIES MODELS R88M-W@ (AC Servomotors) MODELS R88D-WN@-ML2 (AC Servo Drivers) ...
Page 2
... Has the correct product been delivered (i.e., the correct model number and specifications)? • Has the product been damaged in shipping? • Are any screws or bolts loose? NOTICE R88M-W@H-@ R88M-W@T-@ ...
Page 3
... WITH BUILT-IN MECHATROLINK-II COMMUNICATIONS USER’S MANUAL OMNUC W AC SERVOMOTORS/SERVO DRIVERS SERIES MODELS R88M-W@ (AC Servomotors) MODELS R88D-WN@-ML2 (AC Servo Drivers) ...
Page 4
...
Page 5
... OMRON. No patent liability is assumed with respect to the use of the information contained herein. Moreover, because OMRON is con- stantly striving to improve its high-quality products, the information contained in this manual is subject to change without notice ...
Page 6
...
Page 7
... Make sure that these protective covers are on the product before use. Consult your OMRON representative when using the product after a long period of storage. !WARNING Always connect the frame ground terminals of the Servo Driver and the Servomo- tor to a class-3 ground (to 100 Ω ...
Page 8
Do not store or install the product in the following places. Doing so may result in fire, electric shock, or damage to the product. • Locations subject to direct sunlight. • Locations subject to temperatures or humidity outside the ...
Page 9
Be sure to wire correctly and securely. Not doing so may result in motor runaway, injury, or malfunction. !Caution Be sure that all the mounting screws, terminal screws, and cable connector screws are tightened to the torque specified in ...
Page 10
When an alarm occurs, remove the cause, reset the alarm after confirming safety, and then resume operation. Not doing so may result in injury. !Caution Do not use the built-in brake of the Servomotor for ordinary braking. Doing so ...
Page 11
Warning Labels Warning labels are pasted on the product as shown in the following illustration. Be sure to follow the instructions given there. Precautions for Safe Use Dispose of the product and batteries according to local ordinances as they apply. ...
Page 12
...
Page 13
... LOSS OF PROFITS OR COMMERCIAL LOSS IN ANY WAY CONNECTED WITH THE PRODUCTS, WHETHER SUCH CLAIM IS BASED ON CONTRACT, WARRANTY, NEGLIGENCE, OR STRICT LIABILITY event shall the responsibility of OMRON for any act exceed the individual price of the product on which liability is asserted EVENT SHALL OMRON BE RESPONSIBLE FOR WARRANTY, REPAIR, OR OTHER CLAIMS ...
Page 14
... Application Considerations OMRON shall not be responsible for conformity with any standards, codes, or regulations that apply to the combination of products in the customer's application or use of the products. At the customer's request, OMRON will provide applicable third party certification documents identifying ratings and limitations of use that apply to the products. This information by itself is not sufficient for a complete determination of the suitability of the products in combination with the end product, machine, system, or other application or use ...
Page 15
... Performance data given in this manual is provided as a guide for the user in determining suitability and does not constitute a warranty. It may represent the result of OMRON's test conditions, and the users must correlate it to actual application requirements. Actual performance is subject to the OMRON Warranty and Limitations of Liability. The information in this manual has been carefully checked and is believed to be accurate ...
Page 16
...
Page 17
Chapter 1. Introduction 1-1 Features. ...
Page 18
Chapter 6. Appendix . . . . . . . . . . . . . . . . . . . . . . . . . . . . . . . . . . . . . ...
Page 19
Introduction 1-1 Features 1-2 System Configuration 1-3 Servo Driver Nomenclature 1-4 Applicable Standards and Models 1-5 System Block Diagrams Chapter 1 ...
Page 20
Introduction 1-1 Features OMNUC W-series AC Servo Drivers with built-in MECHATROLINK-II Communications are designed specifically for use with the MECHATROLINK-II high-speed motion field network. Combining these Servo Drivers with MECHATROLINK-II-compatible Motion Control Units (CS1W-MCH71 or CJ1W-MCH71) or Position Control Units ...
Page 21
Introduction Regenerative Power Processing ■ In addition to the built-in regenerative power processing function using regeneration resistance, external regeneration resistance can also be connected, allowing the W Series to be used for appli- cations with high regenerative energy on vertical ...
Page 22
... Controller (MECHATROLINK-II Type) SYSMAC CS1 Programmable Controller 1-4 MECHATRO LINK-II CJ1W-NCF71 Position Control Unit CJ1W-MCH71 Motion Control Unit MECHATRO LINK-II CS1W-MCH71 Motion Control Unit Chapter 1 R88D-WN@@@-ML2 OMNUC W-series AC Servo Driver with built- in MECHATROLINK-II Communications INC INC ABS ABS R88M-W@ OMNUC W-series AC Servomotor ...
Page 23
Introduction 1-3 Servo Driver Nomenclature DIP Switch Used for MECHATROLINK-II communications settings. Model Number Rotary Switch (SW1) Used for setting MECHATROLINK-II node address. Charge Indicator Lit when the main-circuit is powered. Also, for Servo Drivers less, ...
Page 24
Introduction 1-4 Applicable Standards and Models EC Directives ■ EC Directive Product Low Voltage AC Servo Drivers EN50178 AC Servomotors IEC60034-8 EMC AC Servo Drivers and AC Servo- motors Note Installation under the conditions specified in 3-2-5 Wiring for Conformity ...
Page 25
Introduction 1-5 System Block Diagrams 100 V AC: R88D-WNA5L-ML2/WN01L-ML2/-WL02L-ML2/-WN04L-ML2 ■ Single-phase 100 to 115 V +10%/−15% (50/60 Hz) Noise filter Varistor 1KM L1 L2 Voltage detection Varistor L1C L2C Power Power Open for OFF ON servo alarm 1KM 1Ry 1KM ...
Page 26
Introduction 200 V AC: R88D-WN05H-ML2/WN10H-ML2 ■ Three-phase 200 to 230 V +10%/−15% (50/60 Hz) Noise filter Varistor 1KM Voltage detection Varistor L1C L2C Power Power Open for OFF ON servo alarm 1KM 1Ry 1KM Surge ...
Page 27
Introduction 200 V AC: R88D-WN15H-ML2/-WN20H-ML2/-WN30H-ML2 ■ Three-phase 200 to 230 V +10%/−15% (50/60 Hz) Noise filter Varistor 1KM Voltage detection Varistor L1C L2C Power Power Open for OFF ON servo alarm 1KM 1Ry 1KM Surge ...
Page 28
Introduction 1-10 Chapter 1 ...
Page 29
Standard Models and Specifications 2-1 Standard Models 2-2 Servo Driver and Servomotor Combinations 2-3 External and Mounted Dimensions 2-4 Servo Driver Specifications 2-5 Servomotor Specifications 2-6 Cable and Connector Specifications 2-7 External Regeneration Resistor Specifications 2-8 Absolute Encoder Backup Battery ...
Page 30
... R88A-CRWC0R3C Cable (with Battery) Note In order to use a personal computer to monitor a Servo Driver and set its parame- ters, Computer Monitor Cable and Com- puter Monitor Software are required. Please ask an OMRON representative for details. Absolute Encoder Backup ■ Battery Specifications 1,000 mA·h, 3.6 V ...
Page 31
Standard Models and Specifications Standard Encoder Cables (for ■ Incremental and Absolute Encoders) Specifications For 3,000- R88A-CRWA003C min Servomo- 750 R88A-CRWA005C tors 10 m R88A-CRWA010C 15 m R88A-CRWA015C 20 m R88A-CRWA020C 30 m ...
Page 32
Standard Models and Specifications Specifications Model Without brake 1 R88A-CAWB003S R88A-CAWB003B 5 m R88A-CAWB005S R88A-CAWB005B 10 m R88A-CAWB010S R88A-CAWB010B 15 m R88A-CAWB015S R88A-CAWB015B 20 m R88A-CAWB020S R88A-CAWB020B 30 m R88A-CAWB030S R88A-CAWB030B 40 m R88A-CAWB040S R88A-CAWB040B 50 m ...
Page 33
Standard Models and Specifications Specifications For 3,000-r/ 100 R88A-CRWA003CR min Flat-style R88A-CRWA005CR Servomotors 1 R88A-CRWA010CR 15 m R88A-CRWA015CR 20 m R88A-CRWA020CR 30 m R88A-CRWA030CR 40 m R88A-CRWA040CR 50 m R88A-CRWA050CR For ...
Page 34
Standard Models and Specifications Specifications Model Without brake 1 R88A-CAWD003SR R88A-CAWD003BR R88A-CAWD005SR R88A-CAWD005BR 10 m R88A-CAWD010SR R88A-CAWD010BR 15 m R88A-CAWD015SR R88A-CAWD015BR 20 m R88A-CAWD020SR R88A-CAWD020BR 30 m R88A-CAWD030SR R88A-CAWD030BR 40 m R88A-CAWD040SR R88A-CAWD040BR ...
Page 35
... R88M-W2K010T R88M-W30010H-BS2 R88M-W30010T-B R88M-W60010H-BS2 R88M-W60010T-B R88M-W90010H-BS2 R88M-W90010T-B R88M-W1K210H-BS2 R88M-W1K210T-B R88M-W2K010H-BS2 R88M-W2K010T-B Chapter 2 With absolute encoder Straight shaft with key R88M-W05030T-S1 R88M-W10030T-S1 R88M-W20030T-S1 R88M-W40030T-S1 R88M-W75030T-S1 R88M-W1K030T-S2 R88M-W1K530T-S2 R88M-W2K030T-S2 R88M-W3K030T-S2 R88M-W05030T-BS1 R88M-W10030T-BS1 R88M-W20030T-BS1 R88M-W40030T-BS1 R88M-W75030T-BS1 R88M-W1K030T-BS2 R88M-W1K530T-BS2 R88M-W2K030T-BS2 R88M-W3K030T-BS2 R88M-WP10030T-S1 R88M-WP20030T-S1 R88M-WP40030T-S1 R88M-WP75030T-S1 ...
Page 36
... R88M-W1K530H- R88M-W2K030H- R88M-W3K030H-BO ● 3,000-r/min Flat-style Servomotors Without 200 V 100 W R88M-WP10030H-W brake 200 W R88M-WP20030H-W 400 W R88M-WP40030H-W 750 W R88M-WP75030H-W 1.5 kW R88M-WP1K530H-W With 200 V 100 W R88M-WP10030H-BW brake 200 W R88M-WP20030H-BW 400 W R88M-WP40030H-BW 750 W R88M-WP75030H-BW 1.5 kW R88M-WP1K530H-BW ● 1,000-r/min Servomotors Without 200 V 300 W R88M-W30010H-O ...
Page 37
... Servomotors Specifications Basic model 200 R88M-W05030H/T 100 W R88M-W10030H/T 200 W R88M-W20030H/T 400 W R88M-W40030H/T 750 W R88M-W75030H R88M-W1K030H/T 1.5 kW R88M-W1K530H R88M-W2K030H R88M-W3K030H/T 3,000-r/min Flat-style Servomotors Specifications Basic model 200 V 100 W R88M-WP10030H/T 200 W R88M-WP20030H/T 400 W R88M-WP40030H/T 750 W R88M-WP75030H/T 1.5 kW R88M-WP1K530H/T ...
Page 38
... Basic model 200 V 450 W R88M-W45015T 850 W R88M-W85015T 1.3 kW R88M-W1K315T 1.8 kW R88M-W1K815T Combination Table for Servomotors with Economy Gears ■ Economy Gears are low-cost gears, with a maximum backlash of 45 degrees. The shaft is a straight shaft with key. Models without keys are not available. ...
Page 39
... Standard Models and Specifications 3,000-r/min Flat-style Servomotors Specifications Basic model 200 V 100 W R88M-WP10030H/T 200 W R88M-WP20030H/T 400 W R88M-WP40030H/T 750 W R88M-WP75030H/T 1.5 kW R88M-WP1K530H/T Gear (deceleration rate) 1/5 1/9 1/15 1/25 -G05CJ -G09CJ -G15C -G25CJ Yes Yes Yes Yes Yes Yes Yes Yes Yes ...
Page 40
... R88M-W1K030H-BG09BJ R88M-W1K030T-G09BJ R88M-W1K030H-BG20BJ R88M-W1K030T-G20BJ R88M-W1K030H-BG29BJ R88M-W1K030T-G29BJ R88M-W1K030H-BG45BJ R88M-W1K030T-G45BJ R88M-W1K530H-BG05BJ R88M-W1K530T-G05BJ R88M-W1K530H-BG09BJ R88M-W1K530T-G09BJ R88M-W1K530H-BG20BJ R88M-W1K530T-G20BJ R88M-W1K530H-BG29BJ R88M-W1K530T-G29BJ R88M-W1K530H-BG45BJ R88M-W1K530T-G45BJ R88M-W2K030H-BG05BJ R88M-W2K030T-G05BJ R88M-W2K030H-BG09BJ R88M-W2K030T-G09BJ R88M-W2K030H-BG20BJ R88M-W2K030T-G20BJ R88M-W2K030H-BG29BJ R88M-W2K030T-G29BJ R88M-W2K030H-BG45BJ R88M-W2K030T-G45BJ R88M-W3K030H-BG05BJ R88M-W3K030T-G05BJ R88M-W3K030H-BG09BJ R88M-W3K030T-G09BJ R88M-W3K030H-BG20BJ R88M-W3K030T-G20BJ R88M-W3K030H-BG29BJ R88M-W3K030T-G29BJ R88M-W3K030H-BG45BJ R88M-W3K030T-G45BJ Chapter 2 With absolute encoder ...
Page 41
... R88M-WP20030H-G33BJ R88M-WP20030H-BG33BJ R88M-WP20030T-G33BJ R88M-WP20030T-BG33BJ 400 W 1/5 R88M-WP40030H-G05BJ R88M-WP40030H-BG05BJ R88M-WP40030T-G05BJ R88M-WP40030T-BG05BJ 1/11 R88M-WP40030H-G11BJ R88M-WP40030H-BG11BJ R88M-WP40030T-G11BJ R88M-WP40030T-BG11BJ 1/21 R88M-WP40030H-G21BJ R88M-WP40030H-BG21BJ R88M-WP40030T-G21BJ R88M-WP40030T-BG21BJ 1/33 R88M-WP40030H-G33BJ R88M-WP40030H-BG33BJ R88M-WP40030T-G33BJ R88M-WP40030T-BG33BJ 750 W 1/5 R88M-WP75030H-G05BJ R88M-WP75030H-BG05BJ R88M-WP75030T-G05BJ R88M-WP75030T-BG05BJ 1/11 R88M-WP75030H-G11BJ R88M-WP75030H-BG11BJ R88M-WP75030T-G11BJ R88M-WP75030T-BG11BJ 1/21 R88M-WP75030H-G21BJ R88M-WP75030H-BG21BJ R88M-WP75030T-G21BJ R88M-WP75030T-BG21BJ 1/33 R88M-WP75030H-G33BJ R88M-WP75030H-BG33BJ R88M-WP75030T-G33BJ R88M-WP75030T-BG33BJ 1 ...
Page 42
... R88M-W60010T-G20BJ R88M-W60010H-BG29BJ R88M-W60010T-G29BJ R88M-W60010H-BG45BJ R88M-W60010T-G45BJ R88M-W90010H-BG05BJ R88M-W90010T-G05BJ R88M-W90010H-BG09BJ R88M-W90010T-G09BJ R88M-W90010H-BG20BJ R88M-W90010T-G20BJ R88M-W90010H-BG29BJ R88M-W90010T-G29BJ R88M-W90010H-BG45BJ R88M-W90010T-G45BJ R88M-W1K210H-BG05BJ R88M-W1K210T-G05BJ R88M-W1K210H-BG09BJ R88M-W1K210T-G09BJ R88M-W1K210H-BG20BJ R88M-W1K210T-G20BJ R88M-W1K210H-BG29BJ R88M-W1K210T-G29BJ R88M-W1K210H-BG45BJ R88M-W1K210T-G45BJ R88M-W2K010H-BG05BJ R88M-W2K010T-G05BJ R88M-W2K010H-BG09BJ R88M-W2K010T-G09BJ R88M-W2K010H-BG20BJ R88M-W2K010T-G20BJ Model With brake Without brake --- R88M-W45015T-G05BJ --- R88M-W45015T-G09BJ --- R88M-W45015T-G20BJ --- R88M-W45015T-G29BJ --- ...
Page 43
... R88M-WP10030H-G09CJ R88M-WP10030H-BG09CJ R88M-WP10030T-G09CJ R88M-WP10030T-BG09CJ 1/15 R88M-WP10030H-G15CJ R88M-WP10030H-BG15CJ R88M-WP10030T-G15CJ R88M-WP10030T-BG15CJ 1/25 R88M-WP10030H-G25CJ R88M-WP10030H-BG25CJ R88M-WP10030T-G25CJ R88M-WP10030T-BG25CJ 200 W 1/5 R88M-WP20030H-G05CJ R88M-WP20030H-BG05CJ R88M-WP20030T-G05CJ R88M-WP20030T-BG05CJ 1/9 R88M-WP20030H-G09CJ R88M-WP20030H-BG09CJ R88M-WP20030T-G09CJ R88M-WP20030T-BG09CJ 1/15 R88M-WP20030H-G15CJ R88M-WP20030H-BG15CJ R88M-WP20030T-G15CJ R88M-WP20030T-BG15CJ 1/25 R88M-WP20030H-G25CJ R88M-WP20030H-BG25CJ R88M-WP20030T-G25CJ R88M-WP20030T-BG25CJ 400 W 1/5 R88M-WP40030H-G05CJ R88M-WP40030H-BG05CJ R88M-WP40030T-G05CJ R88M-WP40030T-BG05CJ 1/9 ...
Page 44
... R88M-W1K210H R88M-W2K010H-@ 2-16 With absolute encoder R88M-W05030T-@ R88D-WNA5H-ML2/A5L-M2 R88M-W10030T-@ R88D-WN01H-ML2/01L-ML2 R88M-W20030T-@ R88D-WN02H-ML2/02L-ML2 R88M-W40030T-@ R88D-WN04H-ML2/04L-ML2 R88M-W75030T-@ R88D-WN08H-ML2 R88M-W1K030T-@ R88D-WN10H-ML2 R88M-W1K530T-@ R88D-WN15H-ML2 R88M-W2K030T-@ R88D-WN20H-ML2 R88M-W3K030T-@ R88D-WN30H-ML2 With absolute encoder R88M-WP10030T-@ R88D-WN01H-ML2/01L-ML2 R88M-WP20030T-@ R88D-WN02H-ML2/02L-ML2 R88M-WP40030T-@ R88D-WN04H-ML2/04L-ML2 R88M-WP75030T-@ R88D-WN08H-ML2 R88M-WP1K530T-@ R88D-WN15H-ML2 With absolute encoder ...
Page 45
... Standard Models and Specifications 1,500-r/min Servomotors and Servo Drivers ■ Voltage Servomotor Rated With incremental output encoder 200 V 450 W --- 850 W --- 1.3 kW --- 1.8 kW --- With absolute encoder R88M-W45015T-@ R88D-WN05H-ML2 R88M-W85015T-@ R88D-WN10H-ML2 R88M-W1K315T-@ R88D-WN15H-ML2 R88M-W1K815T-@ R88D-WN20H-ML2 Chapter 2 Servo Driver 2-17 ...
Page 46
Standard Models and Specifications 2-3 External and Mounted Dimensions 2-3-1 AC Servo Drivers Single-phase 100 V: R88D-WNA5L-ML2/-WN01L-ML2/-WN02L-ML2 ■ (50 to 200 W) Single-phase 200 V: R88D-WNA5H-ML2/-WN01H-ML2/-WN02H-ML2 (50 to 200 W) ● Wall Mounting External dimensions SW1 C N CN6 6 ...
Page 47
Standard Models and Specifications ● Front Panel Mounting (Using Mounting Brackets) External dimensions (7.5) 1.5 36 19.5 (25.5) 5 dia. CN6 SW1 CHARGE A/B L1 CN3 L2 L1C L2C B1/ + CN1 B2 Terminal ...
Page 48
Standard Models and Specifications ● Front Panel Mounting (Using Mounting Brackets) External dimensions (15.5) 18.5 36 36.5 (33.5) 5 dia. Air flow Terminal Block CN6 CN3 Air flow CN1 CN2 CN4 Air flow 5 Ground terminals 70 Two M4 screws ...
Page 49
Standard Models and Specifications ● Front Panel Mounting (Using Mounting Brackets) External dimensions (7.5) 21.5 36 (25.5) 39.5 5 dia. CN6 CN3 CN1 Terminal Block CN2 CN4 Ground terminals Two M4 5 screws Single-phase 200 VAC: R88D-WN08HML2 ...
Page 50
Standard Models and Specifications Front Panel Mounting (Using Mounting Brackets) ● External dimensions (15.5) 18.5 36 (33.5) 36.5 5 dia. Air flow Terminal CN6 Block CN3 Air flow CN1 CN2 CN4 Air flow 5 Ground terminals 70 Two M4 screws ...
Page 51
Standard Models and Specifications ● Front Panel Mounting (Using Mounting Brackets) External Dimensions Air flow CHARGE SW1 L1C L2C B1 Terminal B3 1 blocks - - 2 Ground terminals U V Two M4 screws W ...
Page 52
Standard Models and Specifications Front Panel Mounting (Using Mounting Brackets) ● External dimensions 100 2 Air flow Terminal CHARGE Block SW1 A/B 5 Air flow 2 Ground terminals Two M4 screws 102.2 2-24 Two, 5 dia. ...
Page 53
... Standard Models and Specifications 2-3-2 AC Servomotors 3,000-r/min Servomotors without a Brake ■ ● 200 V AC: 50 W/100 W R88M-W05030H(-S1)/-W10030H(-S1) [Incremental] R88M-W05030T(-S1)/-W10030T(-S1) [Absolute] 300 ±30 6 dia. 7 dia. 300 ± 3,000-r/min Servomotors with a Brake ■ ● 200 V AC: 50 W/100 W R88M-W05030H-B(S1)/-W10030H-B(S1) [Incremental] R88M-W05030T-B(S1)/-W10030T-B(S1) [Absolute] 300 ± ...
Page 54
... Standard Models and Specifications 3,000-r/min Servomotors without a Brake ■ ● 200 V AC: 200 W/400 W/750 W R88M-W20030H(-S1)/-W40030H(-S1)/-W75030H(-S1) [Incremental] R88M-W20030T(-S1)/-W40030T(-S1)/-W75030T(-S1) [Absolute] 300 ±30 6 dia. 7 dia. 13 300 ± 2-26 Model R88M-W20030@-@ R88M-W40030@-@ R88M-W75030@-@ 21.5 Four, Z dia Chapter 2 Dimensions (mm 96 50h7 6 5 ...
Page 55
... Standard Models and Specifications 3,000-r/min Servomotors with a Brake ■ ● 200 V AC: 200 W/400 W/750 W R88M-W20030H-B(S1)/-W40030H-B(S1)/-W75030H-B(S1) [Incremental] R88M-W20030T-B(S1)/-W40030T-B(S1)/-W75030T-B(S1) [Absolute] 6 dia. 7 dia 300 ±30 Model R88M-W20030@-B@ R88M-W40030@-B@ R88M-W75030@-B@ 300 ±30 21.5 Four, Z dia Chapter 2 Dimensions (mm 136 50h7 6 5.5 ...
Page 56
... Standard Models and Specifications 3,000-r/min Servomotors without a Brake ■ ● 200 V AC: 1 kW/1.5 kW/2 kW/3 kW R88M-W1K030H(-S2)/-W1K5030H(-S2)/-W2K030H(-S2)/-W3K030H(-S2) [Incremental] R88M-W1K030T(-S2)/-W1K5030T(-S2)/-W2K030T(-S2)/-W3K030T(-S2) [Absolute] LL KB1 KB2 Model LL LR KB1 KB2 KL1 R88M-W1K030@-@ 149 76 128 R88M-W1K530@-@ 175 45 102 154 96 R88M-W2K030@-@ 198 ...
Page 57
... R88M-W1K030T-B(S2)/-W1K5030T-B(S2)/-W2K030T-B(S2)/-W3K030T-B(S2) [Absolute] LL KB2 Model LL LR KB1 KB2 KL1 R88M-W1K030@-B@ 193 67 171 R88M-W1K530@-B@ 219 45 93 197 102 R88M-W2K030@-B@ 242 116 220 R88M-W3K030@-B@ 237 63 114 216 119 Note: The external dimensions are the same for IP67 (waterproof) models (-BO@). KB1 Dimensions (mm) KL2 C D1 ...
Page 58
... V AC: 100 W/200 W/400 W/750 W/1.5 kW R88M-WP10030H(-S1)/-WP20030H(-S1)/-WP40030H(-S1)/-WP75030H(-S1)/ -WP1K530H(-S1) [Incremental] R88M-WP10030T(-S1)/-WP20030T(-S1)/-WP40030T(-S1)/-WP75030T(-S1)/ -WP1K530T(-S1) [Absolute] Model Basic servomotor dimensions LL LR R88M-WP10030@-@ 62 25 R88M-WP20030@-@ 67 30 R88M-WP40030@-@ 87 R88M-WP75030@-@ 86.5 40 120 145 110 R88M-WP1K530@-@ 114.5 300 ±30 13 300 ± 2-30 Dimensions (mm) With key (shaft end dimensions) ...
Page 59
... V AC: 100 W/200 W/400 W/750 W/1.5 kW R88M-WP10030H-B(S1)/-WP20030H-B(S1)/-WP40030H-B(S1)/-WP75030H-B(S1)/ -WP1K530H-B(S1) [Incremental] R88M-WP10030T-B(S1)/-WP20030T-B(S1)/-WP40030T-B(S1)/-WP75030T-B(S1)/ -WP1K530T-B(S1) [Absolute] Model Basic servomotor dimensions LL LR R88M-WP10030@- R88M-WP20030@-B@ 98.5 30 R88M-WP40030@-B@ 118.5 R88M-WP75030@-B@ 120 40 120 145 110 R88M-WP1K530@-B@ 148 300 ±30 13 300 ± Dimensions (mm) With key (shaft end dimensions) C ...
Page 60
... R88M-W30010T(-S2)/-W60010T(-S2)/-W90010T(-S2)/-W1K210T(-S2)/-W2K010T(-S2) [Absolute] LL KB1 KB2 Model (mm KB1 KB2 R88M-W30010@-@ 138 65 117 R88M-W60010@-@ 161 58 88 140 R88M-W90010@-@ 185 112 164 R88M-W1K210@-@ 166 89 144 79 R88M-W2K010@-@ 192 115 170 Note: The external dimensions are the same for IP67 (waterproof) models (-O@). 2- Dimensions (mm) KL1 KL2 ...
Page 61
... R88M-W30010T-B(S2)/-W60010T-B(S2)/-W90010T-B(S2)/-W1K210T-B(S2)/ -W2K010T-B(S2) [Absolute] LL KB2 Model (mm KB1 KB2 R88M-W30010@-B@ 176 56 154 R88M-W60010@-B@ 199 58 79 177 R88M-W90010@-B@ 223 103 201 R88M-W1K210@-B@ 217 79 195 79 R88M-W2K010@-B@ 243 105 221 Note: The external dimensions are the same for IP67 (waterproof) models (-BO@). KB1 Dimensions (mm) KL1 KL2 ...
Page 62
... Standard Models and Specifications 1,500-r/min Servomotors without a Brake ■ ● 200 V AC: 450 W/850 W/1.3 kW/1.8 kW R88M-W45015T(-S2)/-W85015T(-S2)/-W1K315T(-S2)/-W1K815T(-S2) [Absolute] LL KB1 KB2 Model (mm KB1 KB2 R88M-W45015T-@ 138 65 117 R88M-W85015T-@ 161 58 88 140 R88M-W1K315T-@ 185 112 164 R88M-W1K815T-@ 166 79 89 144 Note: The external dimensions are the same for IP67 (waterproof) models (O@) ...
Page 63
... Standard Models and Specifications 1,500-r/min Servomotors with a Brake ■ ● 200 V AC: 450 W/850 W/1.3 kW/1.8 kW R88M-W45015T-B(S2)/-W85015T-B(S2)/-W1K315T-B(S2)/-W1K815T-B(S2) [Absolute] LL KB2 Model (mm KB1 KB2 R88M-W45015T-B@ 176 56 154 R88M-W85015T-B@ 199 58 79 177 R88M-W1K315T-B@ 223 103 201 R88M-W1K815T-B@ 217 79 79 195 Note: The external dimensions are the same for IP67 (waterproof) models (-BO@). ...
Page 64
... R88M-W20030@-@G11BJ 1/21 R88M-W20030@-@G21BJ 1/33 R88M-W20030@-@G33BJ 400 W 1/5 R88M-W40030@-@G05BJ 2 1/11 R88M-W40030@-@G11BJ 1/21 R88M-W40030@-@G21BJ 1/33 R88M-W40030@-@G33BJ 750 W 1/5 R88M-W75030@-@G05BJ 2 1/11 R88M-W75030@-@G11BJ 1/21 R88M-W75030@-@G21BJ 1/33 R88M-W75030@-@G33BJ Note The values in parentheses are reference values. ...
Page 65
... W 10 R88M-W20030@-@G11BJ 1/11 12 R88M-W20030@-@G21BJ 1/21 12 R88M-W20030@-@G33BJ 1/33 10 R88M-W40030@-@G05BJ 1/5 400 W 12 R88M-W40030@-@G11BJ 1/11 16 R88M-W40030@-@G21BJ 1/21 16 R88M-W40030@-@G33BJ 1/33 12 R88M-W75030@-@G05BJ 1/5 750 W 16 R88M-W75030@-@G11BJ 1/11 20 R88M-W75030@-@G21BJ 1/21 20 R88M-W75030@-@G33BJ 1/33 Key dimensions ...
Page 66
... R88M-W1K530@-@G29BJ 1/45 R88M-W1K530@-@G45BJ 2 kW 1/5 R88M-W2K030@-@G05BJ 1 1/9 R88M-W2K030@-@G09BJ 2 1/20 R88M-W2K030@-@G20BJ 1/29 R88M-W2K030@-@G29BJ 1/45 R88M-W2K030@-@G45BJ 3 kW 1/5 R88M-W3K030@-@G05BJ 2 1/9 R88M-W3K030@-@G09BJ 1/20 R88M-W3K030@-@G20BJ 1/29 R88M-W3K030@-@G29BJ 1/45 R88M-W3K030@-@G45BJ Diagram 1 LL 2-38 ...
Page 67
... R88M-W1K530@-@G09BJ 1/9 R88M-W1K530@-@G20BJ 1/20 R88M-W1K530@-@G29BJ 1/29 R88M-W1K530@-@G45BJ 1/45 R88M-W2K030@-@G05BJ 1 R88M-W2K030@-@G09BJ 1/9 R88M-W2K030@-@G20BJ 1/20 R88M-W2K030@-@G29BJ 1/29 R88M-W2K030@-@G45BJ 1/45 R88M-W3K030@-@G05BJ 1 R88M-W3K030@-@G09BJ 1/9 R88M-W3K030@-@G20BJ 1/20 R88M-W3K030@-@G29BJ 1/29 R88M-W3K030@-@G45BJ 1/ Six, Z dia. ...
Page 68
... R88M-WP20030@-@G21BJ 1/33 R88M-WP20030@-@G33BJ 400 W 1/5 R88M-WP40030@-@G05BJ 1 1/11 R88M-WP40030@-@G11BJ 1/21 R88M-WP40030@-@G21BJ 1/33 R88M-WP40030@-@G33BJ 750 W 1/5 R88M-WP75030@-@G05BJ 1 1/11 R88M-WP75030@-@G11BJ 1/21 R88M-WP75030@-@G21BJ 1/33 R88M-WP75030@-@G33BJ 1.5 kW 1/5 R88M-WP1K530@-@G05BJ 1 1/11 R88M-WP1K530@-@G11BJ 1/21 R88M-WP1K530@-@G21BJ 2 1/33 R88M-WP1K530@-@G33BJ Note The values in parentheses are reference values ...
Page 69
... R88M-WP20030@-@G33BJ 1/33 10 R88M-WP40030@-@G05BJ 1/5 12 R88M-WP40030@-@G11BJ 1/11 16 R88M-WP40030@-@G21BJ 1/21 16 R88M-WP40030@-@G33BJ 1/33 12 R88M-WP75030@-@G05BJ 1/5 16 R88M-WP75030@-@G11BJ 1/11 20 R88M-WP75030@-@G21BJ 1/21 20 R88M-WP75030@-@G33BJ 1/33 16 R88M-WP1K530@-@G05BJ 1/5 20 R88M-WP1K530@-@G11BJ 1/11 20 R88M-WP1K530@-@G21BJ 1/21 20 R88M-WP1K530@-@G33BJ 1/33 M (Effective depth Four, Z dia ...
Page 70
... R88M-W90010@-@G05BJ 1/9 R88M-W90010@-@G09BJ 1/20 R88M-W90010@-@G20BJ 1/29 R88M-W90010@-@G29BJ 1/45 R88M-W90010@-@G45BJ 1.2 kW 1/5 R88M-W1K210@-@G05BJ 1/9 R88M-W1K210@-@G09BJ 1/20 R88M-W1K210@-@G20BJ 1/29 R88M-W1K210@-@G29BJ 1/45 R88M-W1K210@-@G45BJ 2 kW 1/5 R88M-W2K010@-@G05BJ 1/9 R88M-W2K010@-@G09BJ 1/20 R88M-W2K010@-@G20BJ ...
Page 71
... R88M-W90010@-@G05BJ 1/5 900 W R88M-W90010@-@G09BJ 1/9 R88M-W90010@-@G20BJ 1/20 R88M-W90010@-@G29BJ 1/29 R88M-W90010@-@G45BJ 1/45 R88M-W1K210@-@G05BJ 1/5 1.2 kW R88M-W1K210@-@G09BJ 1/9 R88M-W1K210@-@G20BJ 1/20 R88M-W1K210@-@G29BJ 1/29 R88M-W1K210@-@G45BJ 1/45 R88M-W2K010@-@G05BJ 1 R88M-W2K010@-@G09BJ 1/9 R88M-W2K010@-@G20BJ 1/20 ...
Page 72
... R88M-W85015T-@G20BJ 1/29 R88M-W85015T-@G29BJ 1/45 R88M-W85015T-@G45BJ 1.3 kW 1/5 R88M-W1K315T-@G05BJ 1/9 R88M-W1K315T-@G09BJ 1/20 R88M-W1K315T-@G20BJ 1/29 R88M-W1K315T-@G29BJ 1/45 R88M-W1K315T-@G45BJ 1.8 kW 1/5 R88M-W1K815T-@G05BJ 1/9 R88M-W1K815T-@G09BJ 1/20 R88M-W1K815T-@G20BJ 1/29 R88M-W1K815T-@G29BJ Diagram 1 LL 2-44 ...
Page 73
... W R88M-W85015T-@G09BJ 1/9 R88M-W85015T-@G20BJ 1/20 R88M-W85015T-@G29BJ 1/29 R88M-W85015T-@G45BJ 1/45 R88M-W1K315T-@G05BJ 1/5 1.3 kW R88M-W1K315T-@G09BJ 1/9 R88M-W1K315T-@G20BJ 1/20 R88M-W1K315T-@G29BJ 1/29 R88M-W1K315T-@G45BJ 1/45 R88M-W1K815T-@G05BJ 1/5 1.8 kW R88M-W1K815T-@G09BJ 1/9 R88M-W1K815T-@G20BJ 1/20 R88M-W1K815T-@G29BJ 1/ Six, Z dia ...
Page 74
... R88M-W75030@-@G25CJ Model 100 W 1/5 R88M-W10030@-@G05CJ 22 1/9 R88M-W10030@-@G09CJ 22 1/15 R88M-W10030@-@G15CJ 22 1/25 R88M-W10030@-@G25CJ 33 200 W 1/5 R88M-W20030@-@G05CJ 22 1/9 R88M-W20030@-@G09CJ 33 1/15 R88M-W20030@-@G15CJ 33 1/25 R88M-W20030@-@G25CJ 33 400 W 1/5 R88M-W40030@-@G05CJ 33 1/9 R88M-W40030@-@G09CJ 33 1/15 R88M-W40030@-@G15CJ 33 1/25 R88M-W40030@-@G25CJ ...
Page 75
Standard Models and Specifications Diagram Diagram Four, Z dia. F (Effective depth Four, Z dia. F (Effective depth Chapter 2 Key dimensions QK t1 ...
Page 76
... Model 100 W 1/5 R88M-WP10030@-@G05CJ 22 1/9 R88M-WP10030@-@G09CJ 22 1/15 R88M-WP10030@-@G15CJ 22 1/25 R88M-WP10030@-@G25CJ 33 200 W 1/5 R88M-WP20030@-@G05CJ 22 1/9 R88M-WP20030@-@G09CJ 33 1/15 R88M-WP20030@-@G15CJ 33 1/25 R88M-WP20030@-@G25CJ 33 400 W 1/5 R88M-WP40030@-@G05CJ 33 1/9 R88M-WP40030@-@G09CJ 33 1/15 R88M-WP40030@-@G15CJ 33 1/25 R88M-WP40030@-@G25CJ 43 750 W ...
Page 77
Standard Models and Specifications Diagram Four, Z dia. (Effective depth × Chapter 2 Key dimensions 2-49 ...
Page 78
Standard Models and Specifications 2-4 Servo Driver Specifications R88D-WN@-ML2/OMNUC W-series AC Servo Drivers (with Built-in ■ MECHATROLINK-II Communications) Referring to 2-2 Servo Driver and Servomotor Combinations, select a Servo Driver to match the Ser- vomotor that is being used. 2-4-1 ...
Page 79
... Main circuits value Control circuits Control method Inverter method PWM frequency Weight Maximum applicable Servomotor wattage Applicable 3,000-r/min [Incremental] W05030H Servomotor [Absolute] (R88M-) 3,000-r/min [Incremental] --- Flat-style [Absolute] 1,000-r/min [Incremental] --- [Absolute] 1,500-r/min [Absolute] Performance Speed control range Load fluctuation rate Voltage fluctuation rate Temperature fluctuation rate ± ...
Page 80
... Heating Main circuits value Control circuits PWM frequency Weight Maximum applicable Servomotor wattage Applica- 3,000-r/ [Incremen- ble Servo- min tal] motor [Absolute] W05030T (R88M-) 3,000-r/ [Incremen- min Flat- tal] style [Absolute] --- 1,000-r/ [Incremen- min tal] [Absolute] --- 1,500-r/ [Absolute] --- min Control method ...
Page 81
... Main circuits value Control circuits PWM frequency Weight Maximum applicable Servomotor wattage Applica- 3,000-r/ [Incremen- ble Servo- min tal] motor [Absolute] --- (R88M-) 3,000-r/ [Incremen- min Flat- tal] type [Absolute] --- 1,000-r/ [Incremen- min tal] [Absolute] W30010T 1,500-r/ [Absolute] W45015T min Control method ...
Page 82
Standard Models and Specifications Protective and Diagnostic Functions ■ Error detection function Parameter checksum error 1 The Servo Driver's internal parameter data is abnormal. Parameter format error 1 The Servo Driver's internal parameter data is abnormal. System parameter checksum The ...
Page 83
Standard Models and Specifications Error detection function Encoder overspeed The encoder rotated at high speed when the power was ON. Encoder overheat The encoder's internal temperature is too high. Current detection error 1 The phase-U current detector is in error. ...
Page 84
Standard Models and Specifications Error detection function DRV alarm 0 Servo Driver DRV error 0 occurred. DRV alarm 1 Servo Driver DRV error 1 occurred. DRV alarm 2 Servo Driver DRV error 2 occurred. Internal command error A command error ...
Page 85
... The following diagram shows the basic system configuration. For details on the number of devices that can be connected, refer to Transmission Time below. Specifications Maximum transmission distance Repeater not required Repeater not required Repeater required OMRON model number JEPMC-REP2000 Chapter Repeater not required Repeater required Repeater required Yaskawa Electric model number ...
Page 86
Standard Models and Specifications ● Connection Example: Connecting to a SYSMAC CS1W-MCH71, CJ1W-MCH71, or CJ1W-NCF71 Host Servo Driver M Servomotor MECHATROLINK-II Communications Setup ■ This section describes the required switch settings for MECHATROLINK-II communications. ● Communications Specifications MECHATROLINK-II communications specifications ...
Page 87
Standard Models and Specifications Transmission time and number of connectable devices Number of connectable 0.25 ms 0.5 ms devices (See note 1 Note 1. When the transmission time is 0.25 ms, set a communications time that is a ...
Page 88
Standard Models and Specifications 2-4-5 I/O Signal Specifications (CN1) External Signal Processing ■ Servo Driver 3 VDC +24VIN Forward rotation drive prohibit 3.3 k POT 7 3.3 k Reverse rotation drive prohibit 3.3 k NOT 8 3.3 ...
Page 89
Standard Models and Specifications Control I/O Signals ■ ● CN1 Control Inputs Pin No. Signal name DEC (9) [SI3] Origin return deceleration switch signal POT (7) [SI1] Forward drive pro- hibit input NOT (8) [SI2)] Reverse drive ...
Page 90
Standard Models and Specifications ● CN1 Control Outputs Pin No. Signal name 3 ALM Alarm output 4 ALMCOM INP1 Positioning com pleted output 1 INP1COM INP2 Positioning com- pleted output 2 INP2COM VCMP Speed ...
Page 91
Standard Models and Specifications CN1: Pin Arrangement ■ Brake inter- lock output 1 BKIR(SO1+) (See note 1.) BKIRCOM 2 (SO1−) Servo alarm 3 ALM output 4 ALMCOM (See note 2 +24VIN Forward drive 7 POT(SI1) prohibit input (See ...
Page 92
Standard Models and Specifications Control Output Circuits ■ ● Position Feedback Output Servo Driver Phase A Output line driver Phase B SN75ALS174NS or equivalent Phase ● Sequence and Alarm Outputs Servo Driver side To other output ...
Page 93
Standard Models and Specifications Forward Drive Prohibit (7: POT) ■ Reverse Drive Prohibit (8: NOT) Note This is the default allocation. For either signal, the drive prohibition is normally disabled. This setting can be changed by Pn50A.3/Pn50B.0. • These two ...
Page 94
Standard Models and Specifications Speed command DEC Latch signal External latch signal 1 (10: EXT1) ■ External latch signal 2 (11: EXT2) External latch signal 3 (12: EXT3) Note This is the default allocation. The EXT1, EXT2, and EXT3 signals ...
Page 95
Standard Models and Specifications Note These outputs are always OFF when the control mode is any mode other than position control. Speed Conformity Output (VCMP) ■ Note As the default setting, the VCMP signal is not allocated allocated ...
Page 96
Standard Models and Specifications Speed Limit Detection Output (VLIMT) ■ Note As the default setting, the VLIMT signal is not allocated allocated in Pn50F.1. • The VLIMT signal is turned ON in either of the following two cases. ...
Page 97
Standard Models and Specifications ● CN2 Connectors Used (6P) Receptacle at Servo Driver 53460-0611 (Molex Japan Co., Ltd.) Cable plug 55100-0670 (Molex Japan Co., Ltd.) 2-4-7 Personal Computer Monitor Connector Specifications (CN3) Pin No. Symbol Signal name 1, 8 TXD+ ...
Page 98
Standard Models and Specifications ● Monitored Items and Scaling Changes Monitored item 1 V per 1,000 r/min; forward rotation: − voltage; reverse rotation: + Servomotor rotation speed voltage 1 V per 1,000 r/min; forward command: − voltage; reverse com- Speed ...
Page 99
... Standard Models and Specifications 2-5 Servomotor Specifications OMNUC W-series AC Servomotors (R88M-W@) ■ There are three kinds of OMNUC W-Series AC Servomotors, as follows: • 3,000-r/min Servomotors • 3,000-r/min Flat-style Servomotors • 1,000-r/min Servomotors • 1,500-r/min Servomotors These Servomotors also have optional specifications, such as shaft type, with or without brake, waterproofing, with or without reduction gears, and so on ...
Page 100
Standard Models and Specifications Item 50 to 750 W Run position All directions Insulation grade Type B Structure Totally-enclosed self-cooling Vibration grade V-15 Mounting method Flange-mounting EC Direc- EMC Direc- EN55011 class A group 1 tives tive EN61000-6-2 Low-voltage IEC60034-8, ...
Page 101
... Standard Models and Specifications 2-5-2 Performance Specifications 3,000-r/min Servomotors ■ ● Performance Specifications Table Model (R88M-) Item Unit Rated output Rated torque* N·m 0.159 Rated rotation speed r/min 3,000 Momentary maximum rota- r/min 5,000 tion speed Momentary maximum N·m 0.477 torque* ...
Page 102
... Standard Models and Specifications Model (R88M-) Item Unit Rated output* W Rated torque* N·m Rated rotation speed r/min Momentary maximum rota- r/min tion speed Momentary maximum N·m torque* Rated current* A (rms) Momentary maximum cur- A (rms) rent* Rotor inertia 2 kg·m 2 (GD /4) Torque constant* N· ...
Page 103
... Repeated usage 0.4 0.318 0.318 0.2 0.19 Continuous usage 0 (r/min) 1000 2000 3000 4000 5000 Chapter 2 Radial load Thrust load End of Servomotor shaft R88M-W20030H/T (200 W) • 2.0 1.91 1.91 1.5 Repeated usage 1.0 0.637 0.637 0.5 0.39 Continuous usage 0 ...
Page 104
... Repeated usage 10 9.3 6.36 6.36 5 3.25 Continuous usage 0 (r/min) 1000 2000 3000 4000 5000 Chapter 2 R88M-W20030H/T (200 W) (N • m) 2.0 1.91 1.91 1.5 Repeated usage 1.0 0.637 0.637 0.5 0.39 Continuous usage 0 (r/min) 1000 2000 3000 4000 5000 ...
Page 105
... Check to see whether there is optimal operation at low temperatures too. !Caution Do not use 2-kW Servomotors within the shaded portions of the following dia- grams. If used in these regions, the Servomotor may heat, causing the encoder to malfunction. R88M-W2K030@ (2 kW) • Effective torque (N m) 6.36 5 ...
Page 106
... Standard Models and Specifications Model (R88M-) Item Unit Allowable thrust load N 49 Weight Without brake kg Approx. 0.7 With brake kg Approx. 0.9 t6 × @250 mm (AI) Radiation shield dimensions (material) Applicable load inertia (See note 6.) Applicable Servo Driver 100 V WN01L-ML2 (R88D-) AC 200 V WN01H-ML2 ...
Page 107
... Repeated usage 4.77 4.77 5 3.0 (4900) Continuous usage 2.4 0 (r/min) 1000 2000 3000 4000 5000 Chapter 2 R88M-WP40030H/T (400 W) (N • m) 4.0 3.82 3.82 (2500) 3.0 Repeated usage 2.0 1.27 1.27 1.0 1.00 0.76 Continuous usage 0 (r/min) 1000 2000 3000 4000 5000 R88M-WP40030H/T (400 W) • ...
Page 108
... An increase in load friction torque visibly increases load inertia. Therefore, even if the Servo Driver parameters are adjusted at a normal temperature, there may not be optimal operation at low tem- peratures. Check to see whether there is optimal operation at low temperatures too. 1,000-r/min Servomotors ■ Performance Specifications Table ● Model (R88M-) Item Unit Rated output* W 300 Rated torque* N· ...
Page 109
... Standard Models and Specifications Model (R88M-) Item Unit Brake Brake inertia 2 2.1 × 10 kg·m specifi- 2 (GD /4) cations ± 10% Excitation voltage V Power consump- W 9.8 tion (at 20 ° C) Current consump- A 0.41 tion (at 20 ° C) Static friction N·m 4.41 min. torque Attraction time ms 180 max ...
Page 110
... R88M-W2K010H/T (2 kW) (N • 44.0 43.0 (1825) 40 35.8 30 Repeated usage 21.6 19 9.7 Continuous usage 0 (r/min) 500 1000 1500 2000 Chapter 2 R88M-W90010H/T (900 W) (N • 19.3 18.8 (1800) 15 12.5 Repeated usage 10 8.8 8.62 5 4.3 Continuous usage 0 (r/min) 500 1000 1500 2000 ...
Page 111
... Standard Models and Specifications !Caution Do not use 900-W or 2-kW Servomotors within the shaded portions of the follow- ing diagrams. If used in these regions, the Servomotor may heat, causing the encoder to malfunction. R88M-W90010@ (900 W) • Effective torque (N m) 8.62 7. Ambient temperature (°C) ■ 1,500-r/min Servomotors ● ...
Page 112
... Standard Models and Specifications Model (R88M-) Item Unit Brake Brake inertia 2 2.1 × 10 kg·m specifi- 2 (GD /4) cations ± 10% Excitation voltage V Power consump- W 9.8 tion (at 20 ° C) Current consump- A 0.41 tion (at 20 ° C) Static friction N·m 4.41 min. torque Attraction time ms 180 max ...
Page 113
... Repeated usage 11.5 10 5.88 5.39 5 Continuous usage 2.70 0 (r/min) 500 1000 1500 2000 2500 3000 Chapter 2 R88M-W1K315T (1.3 kW) • 23.3 22.3 (2770) 20 Repeated usage 17.1 10 8.83 8.34 Continuous usage 4.17 0 (r/min) 500 1000 1500 2000 2500 3000 2-85 ...
Page 114
... Standard Models and Specifications !Caution Do not use 1.3-kW Servomotors within the shaded portions of the following dia- grams. If used in these regions, the Servomotor may overheat, causing the encoder to malfunction. R88M-W1K315T (1.3 kW) • Effective torque (N m) 8.34 7. Ambient temperature (°C) 2-5-3 Specifications for Servomotors with Reduction Gears ■ ...
Page 115
... R88M-W1K530@-@G45BJ 1/5 R88M-W2K030@-@G05BJ 600 1/9 R88M-W2K030@-@G09BJ 333 1/20 R88M-W2K030@-@G20BJ 150 1/29 R88M-W2K030@-@G29BJ 103 1/45 R88M-W2K030@-@G45BJ 1/5 R88M-W3K030@-@G05BJ 600 1/9 R88M-W3K030@-@G09BJ 333 1/20 R88M-W3K030@-@G20BJ 150 1/29 R88M-W3K030@-@G29BJ 103 1/45 R88M-W3K030@-@G45BJ 67 Note 1 ...
Page 116
... R88M-WP40030@-@G11BJ 273 1/21 R88M-WP40030@-@G21BJ 143 1/33 R88M-WP40030@-@G33BJ 91 750 W 1/5 R88M-WP75030@-@G05BJ 600 1/11 R88M-WP75030@-@G11BJ 273 1/21 R88M-WP75030@-@G21BJ 143 1/33 R88M-WP75030@-@G33BJ 91 1.5 kW 1/5 R88M-WP1K530@-@G05BJ 600 1/11 R88M-WP1K530@-@G11BJ 273 1/21 R88M-WP1K530@-@G21BJ 143 1/33 R88M-WP1K530@-@G33BJ 91 Note 1 ...
Page 117
... Note 4. The allowable radial loads are measured in the center of the shaft. ■ 1,500-r/min Servomotors with Standard Reduction Gears (450 W to 1.8 kW) Model rotation 450 W 1/5 R88M-W45015T-@G05BJ 300 1/9 R88M-W45015T-@G09BJ 167 1/20 R88M-W45015T-@G20BJ 75 1/29 R88M-W45015T-@G29BJ 52 1/45 R88M-W45015T-@G45BJ 33 ...
Page 118
... W 1/5 R88M-W20030@-@G05CJ 600 1/9 R88M-W20030@-@G09CJ 333 1/15 R88M-W20030@-@G15CJ 200 1/25 R88M-W20030@-@G25CJ 120 400 W 1/5 R88M-W40030@-@G05CJ 600 1/9 R88M-W40030@-@G09CJ 333 1/15 R88M-W40030@-@G15CJ 200 1/25 R88M-W40030@-@G25CJ 120 750 W 1/5 R88M-W75030@-@G05CJ 600 1/9 ...
Page 119
... R88M-WP20030@-@G25CJ 120 400 W 1/5 R88M-WP40030@-@G05CJ 600 1/9 R88M-WP40030@-@G09CJ 333 1/15 R88M-WP40030@-@G15CJ 200 1/25 R88M-WP40030@-@G25CJ 120 750 W 1/5 R88M-WP75030@-@G05CJ 600 1/9 R88M-WP75030@-@G09CJ 333 1/15 R88M-WP75030@-@G15CJ 200 1/25 R88M-WP75030@-@G25CJ 120 Note 1. The reduction gear inertia indicates the Servomotor shaft conversion value. ...
Page 120
Standard Models and Specifications Item 3,000-r/min Servomotors 50 to 750 W Maximum rotation 5,000 r/min speed +S, − S Output signals Output impedance Conforming to EIA RS-422A. Output based on LTC1485CS or equivalent. Serial communica- Position data, poll sensor, U, ...
Page 121
Standard Models and Specifications 2-6 Cable and Connector Specifications 2-6-1 MECHATROLINK-II Communications Cable Specifications MECHATROLINK Communications Cable (With Connectors at Both ■ Ends and a Core) (FNY-W6003-@@) ● Cable Models Name MECHATROLINK-II Cable MECHATROLINK-II Terminating Resistor ● Connection Configuration and ...
Page 122
Standard Models and Specifications ● Wiring The following example shows the MECHATROLINK-II Communications Cable connections between a host device and Servo Drivers. Position Control Unit 200 V R88D-WN01H-ML2 AC SERVO DRIVER POWER 100 W COM SW1 CHARGE ...
Page 123
... Chapter 2 39 Servo Driver side R88D-WN Connector on Servo Driver Connector plug model 10126-3000VE (Sumitomo 3M) Connector Case model 10326-52A0-008 (Sumitomo 3M) Connector on Connector-Terminal Block Conversion Unit Connector Socket Model XG4M-2030 (OMRON) Strain Relief Model XG4T-2004 (OMRON) Cable AWG28 × AWG28 × 7C, UL2464 2-95 ...
Page 124
Standard Models and Specifications Connector-Terminal Block Conversion Unit (XW2B-20G@) ■ Control input signals from WN-series Servo Drivers (CN1) can be converted to a terminal block by using the Connector-Terminal Block Conversion Unit with the XW2Z-@J-B16 Cable for Connector- Terminal Block ...
Page 125
Standard Models and Specifications ● Terminal Block Model XW2B-20G5 The XW2B-20G5 is a Connector-Terminal Block Conversion Unit with a M3.5 screw terminal block. ● External Dimensions 3.5 7 Two, 3.5-dia. holes 8.5 Note The terminal pitch is 8.5 mm. Precautions ...
Page 126
Standard Models and Specifications ● Terminal Blocks XW2D-20G6 The XW2D-20G6 screw terminal block. ● External Dimensions 79 57 Precautions • When using crimp terminals, use crimp terminals with the following dimensions. Round Crimp Terminals Fork Crimp Terminals ...
Page 127
... Note 3. Note: If Robot Cables are used at a bending radius smaller than the minimum bending radi- us, mechanical malfunctions, ground faults, and other problems may occur due to insulation breakdown. Contact your OMRON representative if you need to use a Robot Cable with a bending radius smaller than the minimum bending radius. ...
Page 128
Standard Models and Specifications ● Power Cables Model Without brake R88A-CAWA@@@SR With brake R88A-CAWA@@@BR Without brake R88A-CAWB@@@SR With brake R88A-CAWB@@@BR Without brake R88A-CAWC@@@SR With brake R88A-CAWC@@@BR Without brake R88A-CAWD@@@SR With brake R88A-CAWD@@@BR ● Encoder Cables Model Minimum bending radius (R) ...
Page 129
... Approx. 1.3 kg 6.8 dia. Approx. 2.5 kg Approx. 3.3 kg Approx. 4.1 kg Outer diameter of sheath 6.5 dia. Approx. 0.4 kg Approx. 0.5 kg Approx. 0.8 kg Approx. 1.1 kg Approx. 1.4 kg 6.8 dia. Approx. 2.6 kg Approx. 3.4 kg Approx. 4 Chapter 2 Weight Weight 43.5 Servomotor R88M-W@ 69.1 Servomotor R88M-W@ 2-101 ...
Page 130
... D S− Length (L) 0.3 Battery holder (provided with battery) Chapter 2 Cable Connector socket: 54280-0609 (Molex Japan) Servomotor Connector plug: 55102-0600 (Molex Japan) Cable Straight plug: N/MS3106B20-29S (JAE Ltd.) Cable plug: N/MS3057-12A (JAE Ltd.) Servomotor Receptacle: MS3102A20-29P (DDK Ltd.) 43.5 Servomotor R88M- ...
Page 131
Standard Models and Specifications ● Wiring R88A-CRWC0R3C Servo Driver Signal No. Red Black Orange BAT+ 3 White/Orange BAT− 4 Open S+ 5 Open/White S− Shell Battery holder Signal No. BAT+ 1 BAT− ...
Page 132
... Connector cap: 350780-1 (Tyco Electronics AMP KK) 1 Phase-U Connector socket: 350689-3 (Tyco Electronics AMP KK) 2 Phase-V Servomotor 3 Phase-W Connector plug: 350779-1 (Tyco Electronics AMP KK) Connector pins 350690-3 (Tyco Electronics AMP KK Connector pin 4: 770210-1 (Tyco Electronics AMP KK) Chapter 2 Weight 27.4 Servomotor R88M-W@ 27.4 Servomotor R88M-W@ ...
Page 133
Standard Models and Specifications For Servomotors with Brakes Servo Driver Red White Blue Green/Yellow Black Brown Cable: AWG20 × 6C UL2464 M4 crimp terminals R88A-CAWB@ ■ The R88A-CAWB@ Cables are for 3,000-r/min Flat-style Servomotors (1.5 kW). ● Cable Models For ...
Page 134
... Pins 350551-3 (Tyco Electronics AMP KK Servomotor Connector plug: 350715-1 (Tyco Electronics AMP KK) 5 Brake Connector pins 350547-6 (Tyco Electronics AMP KK) 6 Brake Connector pin 4: 350669-1 (Tyco Electronics AMP KK) Connector pins 5 and 6: 350690-3 (Tyco Electronics AMP KK) Chapter 2 27.4 Servomotor R88M-W@ 27.4 Servomotor R88M-W@ ...
Page 135
... Approx. 1.9 kg Approx. 2.8 kg Approx. 3.7 kg Approx. 5.6 kg Approx. 7.4 kg Approx. 9.2 kg Outer diameter of sheath 14.5 dia. Approx. 1.1 kg Approx. 1.7 kg Approx. 3.3 kg Approx. 4.9 kg Approx. 6.4 kg Approx. 9.6 kg Approx. 12.7 kg Approx. 15 Chapter 2 Weight Weight 65.9 Servomotor R88M-W@ 69.1 Servomotor R88M-W@ 2-107 ...
Page 136
Standard Models and Specifications ● Wiring For Servomotors without Brakes Servo Driver Red White Blue Green/Yellow Cable: AWG14 × 4C UL2463 M4 crimp terminals For Servomotors with Brakes Servo Driver Red White Blue Green/Yellow Black Brown Cable: AWG14 × 6C ...
Page 137
... Approx. 5.8 kg Approx. 8.6 kg Approx. 11.4 kg Approx. 17.0 kg Approx. 22.6 kg Approx. 28 Servomotor No. Symbol Cable Straight plug: N/MS3106B22-22S (JAE Ltd.) A Phase-U Cable clamp: N/MS3057-12A (JAE Ltd.) B Phase-V Servomotor C Phase-W Receptacle: MS3102A22-22P (DDK Ltd Chapter 2 Weight 69.1 Servomotor R88M-W@ 74.6 Servomotor R88M-W@ 2-109 ...
Page 138
Standard Models and Specifications For Servomotors with Brakes Servo Driver Red White Blue Green/Yellow Black Brown Cable: AWG10 × 6C UL2463 M5 crimp terminals Note Connector-type terminal blocks are used for Servo Drivers of 1 less, as shown ...
Page 139
... Signal H E5V G E0V T BAT+ S BAT− S− Chapter 2 Servomotor R88M-W@ Servomotor R88M-W@ Cable Connector socket: 54280-0609 (Molex Japan) Servomotor Connector plug: 55102-0600 (Molex Japan) Cable Straight plug: N/MS3106B20-29S (JAE Ltd.) Cable plug: N/MS3057-12A (JAE Ltd.) Servomotor Receptacle: MS3102A20-29P (DDK Ltd.) 2-111 ...
Page 140
... Approx. 0.3 kg Approx. 0.6 kg Approx. 0.8 kg Approx. 1.1 kg Approx. 1.7 kg Approx. 2.2 kg Approx. 2.8 kg Outer diameter of sheath 7.0 dia. Approx. 0.2 kg Approx. 0.4 kg Approx. 0.8 kg Approx. 1.1 kg Approx. 1.5 kg Approx. 2.3 kg Approx. 3.0 kg Approx. 3 15.7 Chapter 2 Weight Weight 27.4 Servomotor R88M-W@ ...
Page 141
... Connector pins 350690-3 (Tyco Electronics AMP KK) 5 Brake Connector pin 4: 770210-1 (Tyco Electronics AMP KK) 6 Brake Outer diameter of sheath 9.5 dia. Approx. 0.5 kg Approx. 0.8 kg Approx. 1.5 kg Approx. 2.2 kg Approx. 3.0 kg Approx. 4.5 kg Approx. 5.9 kg Approx. 7.4 kg Chapter 2 27.4 Servomotor R88M-W@ Weight 2-113 ...
Page 142
... Phase-V Pins 350550-6 (Tyco Electronics AMP KK) Pin 4: 350551-3 (Tyco Electronics AMP KK) 3 Phase-W Servomotor 4 FG Connector plug: 350779-1 (Tyco Electronics AMP KK) Connector pins 350547-6 (Tyco Electronics AMP KK) Connector pin 4: 350669-1 (Tyco Electronics AMP KK) Chapter 2 Weight 27.4 Servomotor R88M-W@ 27.4 Servomotor R88M-W@ ...
Page 143
Standard Models and Specifications For Servomotors with Brakes Servo Drivers Red White Blue Green/Yellow Black Brown Cable: AWG15 × 6C UL2586 M4 crimp terminals ■ R88A-CAWC@R The R88A-CAWC@R Cables are for 3,000-r/min Servomotors ( kW), 1,000-r/min Servomotors (300 ...
Page 144
... Phase-U Cable clamp: N/MS3057-10A (JAE Ltd.) B Phase-V Servomotor C Phase-W Receptacle: MS3102A18-10P (DDK Ltd Servomotor No. Symbol Cable Straight plug: N/MS3106B20-15S (JAE Ltd.) A Phase-U Cable clamp: N/MS3057-12A (JAE Ltd.) B Phase-V Servomotor C Phase-W Receptacle: MS3102A20-15P (DDK Ltd Brake F Brake Chapter 2 Servomotor R88M-W@ Servomotor R88M-W@ ...
Page 145
... Approx. 3.3 kg Approx. 4.9 kg Approx. 6.4 kg Approx. 9.5 kg Approx. 12.6 kg Approx. 15.7 kg Outer diameter of sheath 16.5 dia. Approx. 1.7 kg Approx. 2.6 kg Approx. 4.9 kg Approx. 7.2 kg Approx. 9.4 kg Approx. 14.1 kg Approx. 18.7 kg Approx. 23 Chapter 2 Weight Weight 69.1 Servomotor R88M-W@ 74.6 Servomotor R88M-W@ 2-117 ...
Page 146
Standard Models and Specifications ● Wiring For Servomotors without Brakes Servo Driver Red White Blue Green/Yellow Cable: AWG11 × 4C UL2586 M5 crimp terminals For Servomotors with Brakes Servo Driver Red White Blue Green/Yellow Black Brown Cable: AWG11 × 6C ...
Page 147
Standard Models and Specifications ● Wiring Servo Driver Symbol No. Red NM 1 White AM 2 Black GND 3 Black GND 4 Cable: AWG24 × 4C UL1007 Connector socket: DF11-4DS-2C (Hirose Electric) Connector contacts: DF11-2428SCF (Hirose Electric) Computer Monitor Cables ...
Page 148
Standard Models and Specifications Control I/O Connector (R88A-CNW01) ■ This is the connector for connecting to the Servo Driver's Control I/O Connector (CN1). This connec- tor is used when the cable is prepared by the user. ● External Dimensions 39 ...
Page 149
Standard Models and Specifications 2-7 External Regeneration Resistor Specifications If the Servomotor's regenerative energy is excessive, connect an External Regeneration Resistor. R88A-RR22047S External Regeneration Resistor ■ Specifications ■ Model Resistance 47 Ω ± 5% R88A-RR22047S External Dimensions ■ All dimensions ...
Page 150
Standard Models and Specifications 2-8 Absolute Encoder Backup Battery Specifications A backup battery is required when using a Servomotor with an absolute encoder. Install the Battery Unit in the battery holder for the Absolute Encoder Battery Cable (R88A-CRWC0R3C, 0.3 m), ...
Page 151
Standard Models and Specifications Installation ■ R88A-CRWC0R3C Absolute Encoder Battery Cable Battery holder Servo Driver connector Install an R88A-BAT01W Battery. ■ Manufacturing Code The manufacturing code gives the manufacturing date as shown below. The alphanumeric characters have the following meanings. ...
Page 152
Standard Models and Specifications 2-9 Reactor Specifications Connect a DC Reactor to the Servo Driver's DC Reactor connection terminal as a harmonic current control measure. Select a model to match the Servo Driver being used. R88A-PX@ AC/DC Reactors ■ Specifications ...
Page 153
Standard Models and Specifications Model A R88A-PX5052 35 52 R88A-PX5053 35 52 R88A-PX5054 35 52 R88A-PX5056 35 52 R88A-PX5059 50 74 R88A-PX5060 40 59 R88A-PX5061 105 ...
Page 154
Standard Models and Specifications 2-10 MECHATROLINK-II Repeater Specifications The MECHATROLINK-II Repeater is required to extend the MECHATROLINK-II connection distance. FNY-REP2000 ■ Item Cable lengths Controller to Repeater max. Repeater to terminating resistance max. Maximum number of ...
Page 155
Standard Models and Specifications MECHATROLINK-II Repeater Dimensions FNY-REP2000 ■ Dimensions 12 1 4.8 12 Dimensions Mounting on Bottom 50 (97) 77 (20 4 Mounting on Back M4 tap M4 tap Chapter 2 (34) ( ...
Page 156
Standard Models and Specifications Connections An example of connections between the host controller, servo drives, and a Repeater is shown below. R88D -WN0 1H-M L2 200V AC SERVO DRIVER POWER COM 100W SW1 C MECHATROLINK-II N CHAR GE 6 A/B ...
Page 157
System Design and Installation 3-1 Installation Conditions 3-2 Wiring 3-3 Regenerative Energy Absorption 3-4 Adjustments and Dynamic Braking When Load Inertia Is Large Chapter 3 ...
Page 158
System Design and Installation Installation and Wiring Precautions !Caution Do not step on or place a heavy object on the product. Doing so may result in injury. !Caution Do not cover the inlet or outlet ports and prevent any foreign ...
Page 159
System Design and Installation 3-1 Installation Conditions 3-1-1 Servo Drivers Space Around Drivers ■ • Install Servo Drivers according to the dimensions shown in the following illustration to ensure proper heat dispersion and convection inside the panel. Also install a ...
Page 160
System Design and Installation • The service life of a Servo Driver is largely determined by the temperature around the internal elec- trolytic capacitors. The service life of an electrolytic capacitor is affected by a drop in electrolytic vol- ume ...
Page 161
System Design and Installation Connecting to Mechanical Systems ■ • The axial loads for Servomotors are specified in 2-5- 2 Performance Specifications axial load greater than that specified is applied to a Servomotor, it will reduce the service ...
Page 162
... R88M-W1K210@-@ 2 kW R88M-W2K010@-@ 1,500-r/min 1.8 kW R88M-W1K815T-@ With 3,000-r/min 1 kW R88M-W1K030@-B@ brake 1.5 kW R88M-W1K530@- R88M-W2K030@-B@ 1,000-r/min 300 W R88M-W30010@-B@ 600 W R88M-W60010@-B@ 900 W R88M-W90010@-B@ 1,500-r/min 450 W R88M-W45015T-B@ 850 W R88M-W85015T-B@ 1.3 kW R88M-W1K315T-B@ 3,000-r/min 3 kW R88M-W3K030@-B@ 1,000-r/min 1.2 kW R88M-W1K210@- R88M-W2K010@-B@ 1,500-r/min 1.8 kW R88M-W1K815T-B@ 3-6 ...
Page 163
... R88M-W3K030@-@ 1,000-r/min R88M-W30010@-@ to (300 W to 2.0 kW) R88M-W2K010@-@ 1,500-r/min R88M-W45015T-@ to (450 W to 1.8 kW) R88M-W1K815T-@ Water and Drip Resistance ■ The enclosure ratings for the Servomotors are as follows: 3,000-r/min Servomotors (50 to 750 W): IP55 (except for through-shaft parts). 3,000-r/min Servomotors (1 to 3.0 kW): IP67 (except for through-shaft parts). Models are also available with IP67 ratings that include through-shaft parts ...
Page 164
... CHA RGE 6 A Servo Driver Servo Driver R88D-WN@-ML2 CN2 (Encoder Connector) 4 Encoder Cable (See note.) (See note.) Robot Cable 5 Encoder Cable (Refer to page 2-99.) Servomotor Servomotor R88M-W@ Chapter 3 Absolute Encoder Backup Battery Unit R88A-BAT01W Absolute Encoder Battery Cable R88A-CRWC0R3C 0.3 m ...
Page 165
System Design and Installation ● 1. MECHATROLINK-II Cable Special MECHATROLINK-II Cables Use the following cables to connect to MECHATROLINK-II devices. Unit Cable model CJ1W-NCF71 FNY-W6003-A5 CJ1W-MCH71 FNY-W6003-01 CS1W-MCH71 FNY-W6003-03 FNY-W6003-05 FNY-W6003-10 FNY-W6003-20 FNY-W6003-30 Terminating Resistor Use the following terminating resistor ...
Page 166
System Design and Installation ● 4. Encoder Cable Select an Encoder Cable to match the Servomotor that used. Servomotor type 3,000-r/min Servomotors 30 to 750 3.0 kW 3,000-r/min Flat-style 100 W to 1.5 kW ...
Page 167
System Design and Installation ● 6. Computer Monitor Cable A Computer Monitor Cable and Computer Monitor Software are required to set or monitor parame- ters from a personal computer. Name/specifications Computer Monitor For DOS personal Cable computers ● 7. Analog ...
Page 168
... Note 2. Recommended product in 3-2-4 Wiring for Noise Resistance. For conformity to EC Directives, refer to 3-2-5 Wiring for Conformity to EMC Directives. Note 3. Recommended relay: MY Relay (24 V), by OMRON. For example, an MY2 Relay outputs to a 2-A in- ductive load at 24 VDC, making it applicable to all W-series Motors with Brakes. ...
Page 169
... Wiring for Noise Resistance. For conformity to EC Directives, re- fer to 3-2-5 Wiring for Conformity to EMC Directives. Note 3. Recommended relay: MY Relay (24 V), by OMRON. For exam- ple, an MY2 Relay outputs to a 2-A inductive load at 24 VDC, making it applicable to all W-se- ries Motors with Brakes. ...
Page 170
... Wiring for Noise Resistance. For conformity to EC Direc- tives, refer to 3-2-5 Wiring for Conformity to EMC Directives. Note 3. Recommended relay: MY Re- lay (24 V), by OMRON. For ex- ample, an MY2 Relay outputs to a 2-A inductive load at 24 VDC, making it applicable to all W-series Motors with Brakes. ...
Page 171
System Design and Installation 3-2-3 Terminal Block Wiring When wiring a Terminal Block, pay attention to wire sizes, grounding systems, and anti- noise measures. Terminal Block Names and Functions ■ Terminal Name label L1 Main circuit power sup- ply input ...
Page 172
... Frame ground Wire size ( ) Screw size Torque Non-fuse breaker or fuse capacity A (rms) 4 Note 1. Use the same wire sizes for Note 2. Connect special OMRON Power Cable to the Servomotor connection terminals. 200-V AC Input (R88D-WT@H-ML2) ● Model (R88D-) WNA5H- ML2 Item Unit Power supply capacity kVA 0 ...
Page 173
... System Design and Installation Note 1. Use the same wire sizes and tightening torques for Note 2. Connect special OMRON Power Cable to the Servomotor connection terminals. Wire Sizes and Allowable Current ■ The following table shows the allowable current for when there are three wires. ...
Page 174
System Design and Installation 2.Strip the covering off the ends of the wires. Prepare wires of the right sizes, according to the tables provided under Terminal Block Wire Sizes above, and strip off the covering ...
Page 175
... Use a grounding plate for the frame ground for each Unit, as shown in the above diagrams, and ground to a single point. R88D-WN@-ML2 Contactor TB TB Noise filter L1C L2C CN2 R88D-WN@-ML2 Contactor TB TB Noise filter L1C L2C CN2 Chapter 3 R88M-W@ Metal duct Thick power line (3 Machine ground R88M-W@ Metal duct Thick power line (3 Machine ground 3-19 ...
Page 176
System Design and Installation • Use ground lines with a minimum thickness of 3.5 mm lines are as short as possible. • If no-fuse breakers are installed at the top and the power supply line is wired from the lower ...
Page 177
System Design and Installation W Power supply Model voltage Single- 100 WNA5L phase 100 WN01L 100 WN02L 100 WN04L Single- 200 WNA5H phase 200 WN01H 200 WN02H 200 WN04H 200 WN08H Three- 200 WN05H phase 200 WN10H 200 WN15H 200 ...
Page 178
System Design and Installation • The following table shows the noise filters that are recommended for Servomotor output. Maker Model Rated current NEC TOKIN LF-310KA 10 A LF-320KA 20 A LF-350KA 50 A LF-3110KB 110 A Note 1. Servomotor output ...
Page 179
System Design and Installation AC Reactor Connection Example Servo Driver Power supply AC Reactor L1 L2 R88D-WNA5@-ML2 to WN04@-ML2 3-2-5 Wiring for Conformity to EMC Directives When the wiring conditions provided in this section are satisfied, the wiring will conform ...
Page 180
... See note 3. Contactor Noise L3 W filter L1C L2C CN2 Ferrite core Clamp CN1 Ferrite core Clamp Ferrite core Controller 2 , and arrange the wiring so that the ground Chapter 3 Motor built-in device R88M-W@ Metal duct or B Ferrite Ferrite conduit core core M Ferrite core E ...
Page 181
System Design and Installation Correct: Separate input and output AC input AC output Ground • Use twisted-pair cables for the power supply cables whenever possible, or bind the cables. Correct: Properly twisted ...
Page 182
System Design and Installation • Be careful not to let gaps be opened in the control box while tightening down screws. Case Door A B Control box Oil-proof packing Conductive packing Door (interior view) Selecting Components ■ This section explains ...
Page 183
System Design and Installation • When making the selection, add in the current consumption of other controllers, and so on. Servo Driver Inrush Current: The Servo Driver inrush currents are listed in the following table. • With low-speed no-fuse breakers, ...
Page 184
System Design and Installation ● Noise Filters for Power Supply Input Use the following noise filters for the Servo Driver power supply. Servo Driver model Model R88D-WNA5L-ML2 FN2070-6/07 R88D-WN01L-ML2 R88D-WN02L-ML2 FN2070-10/07 R88D-WN04L-ML2 FN2070-16/07 R88D-WNA5H-ML2 FN2070-6/07 R88D-WN01H-ML2 R88D-WN02H-ML2 R88D-WN04H-ML2 FN2070-10/07 R88D-WN08H-ML2 ...
Page 185
System Design and Installation Model FN2070-6/07 113.5 57.5 45.4 FN2070-10/07 156 FN2070-16/07 119 85.5 57.6 • FN258L-7/07, -16/07, -30/07 Noise Filters (by Schaffner) Side View Models Model A B ...
Page 186
... The Servo Driver inrush current is covered in the preceding explanation of no-fuse-breaker selec- tion, and the maximum momentary current is approximately twice the rated current. • The following table shows the recommended contactors. Maker Model Rated current OMRON LC1D09106 11 A LC1D25106 26 A LC1D40116 ...
Page 187
System Design and Installation Note 2. The installation conditions of the power cable and the measurement methods greatly affect these values. Use these values only for reference. The values differ by a factor of approxi- mately 3 between standard breakers ...
Page 188
System Design and Installation 3-3 Regenerative Energy Absorption The Servo Drivers have internal regenerative energy absorption circuitry for absorbing the regenerative energy produced during time such as Servomotor deceleration, and thus preventing the DC voltage from increasing. An overcurrent error ...
Page 189
System Design and Installation Note There is some loss due to winding resistance, so the actual regenerative energy will be approx- imately 90% of the values derived from these equations. • For Servo Driver models with internal capacitors for absorbing ...
Page 190
System Design and Installation Rotation speed at beginning of deceleration [r/min Deceleration torque [N· Torque when falling [N· Deceleration time [s] ...
Page 191
System Design and Installation • Lengthen the operation cycle, i.e., the cycle time (to decrease the average regenerative power). Servo Driver Regenerative energy (J) that can be absorbed by internal capacitor (See note.) R88D-WNA5L-ML2 28.6 R88D-WN01L-ML2 28.6 R88D-WN02L-ML2 28.6 R88D-WN04L-ML2 ...
Page 192
System Design and Installation External Regeneration Resistors ■ ● Specifications Model Resistance 47 Ω ± 5% R88A-RR22047S External Regener- ation Resistor Note The following external regeneration resistors are recommended products from another manu- facturer, Iwaki Musen Kenkyusho Co., Ltd. For ...
Page 193
System Design and Installation Servo Driver Minimum Connection Resistance and External ■ Regeneration Resistor Combinations Servo Driver R88D-WNA5L-ML2 to WN01L-ML2 R88D-WN02L-ML2 to WN04L-ML2 R88D-WNA5H-ML2 to WN01H-ML2 R88D-WN02H-ML2 to WN04H-ML2 R88D-WN05H-ML2 to WN10H-ML2 R88D-WN15H-ML2 R88D-WN20H-ML2 to WN30H-ML2 Wiring External Regeneration Resistance ...
Page 194
System Design and Installation 3-4 Adjustments and Dynamic Braking When Load Inertia Is Large The value that is given for the Servomotor's applicable load inertia is the value that will not damage the Servo Driver's internal circuits (dynamic brake circuit, ...
Page 195
System Design and Installation Servomotor 3,000-r/min Servomotors 400 W 3,000-r/min Servomotors, 750 W 3,000-r/min Servomotors 3,000-r/min Flat-type Servomotors, 100 W 3,000-r/min Flat-type Servomotors, 200 W or 400 W 1,500% max. 3,000-r/min Flat-type Servomotors, ...
Page 196
System Design and Installation 3-40 Chapter 3 ...
Page 197
Operation 4-1 Operational Procedure 4-2 Preparing for Operation 4-3 User Parameters 4-4 Operation Functions 4-5 Trial Operation Procedure 4-6 Making Adjustments 4-7 Advanced Adjustment Functions 4-8 Using Displays 4-9 Using Monitor Output Chapter 4 ...
Page 198
Operation Precautions !Caution Confirm that there will be no effect on the equipment, and then perform a test operation. Not doing so may result in equipment damage. !Caution Check the newly set parameters for proper execution before actually running them. ...
Page 199
Operation 4-1 Operational Procedure After mounting, wiring, and connecting a power supply, check the operation of the Servomotor and Servo Driver. Then make the function settings as required according to the use of the Servomotor and Servo Driver. If the ...
Page 200
Operation 4-2 Preparing for Operation This section explains the procedure following installation and wiring of the Servomotor and Servo Driver, to prepare the mechanical system for operation. It explains what you need to check both before and after turning ON ...